An holistic approach to pipe fabrication
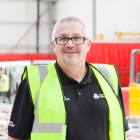
Against the backdrop of Pipe Center having opened a purpose-built branch and fabrication facility for pipework at Basildon, Gary Franklin gives an insight into the many benefits of this evolving approach to pipe fabrication.
The option for prefabrication of pipework is not a new concept. However, we are seeing a general increase in demand for prefabricated pipe systems for a number of reasons, particularly in the public sector and residential, commercial and industrial building-services industries. Traditionally all pipework was completed on-site with contract labour, pipe fitters and welders, or in smaller workshops. Nowadays a fully operational pipe-fabrication facility will see a project evolve from sourcing the required components, through to production of 3D drawings, actual fabrication and installation on-site.
So what is driving this approach?
Helping customers to emerge from the aftermath of the recession has been critical over the last few years. It has meant that more companies have scaled down their own facilities, resulting in the lack of hot works on site. Furthermore, a decline in skilled workforce and labour, a call for improved ease of installation, security of cost and waste management have all played an integral role in building-services providers looking for new ways to remain operational and, ultimately, profitable.
A key benefit to outsourcing the fabrication of piping systems is the access to innovative tools, processes and materials that consistently evolve to increase efficiencies.
For example, in our new facility at Basildon we have been able to introduce the latest automated welding Fronius equipment for metal inert gas (MIG) welding, an investment exceeding £20 000 to support the fabrication of pipe with the highest quality and speed of welding capabilities. The 3 in butt weld is reduced to root fill and cap, which reduces welding time by around 50%. The controlled welding arc and wire feed ratio significantly improves welding time, as well as producing a cleaner weld and welding environment. There are also increased consistencies with the weld profile and penetration meaning a significant reduction in consumables.
The investment into the Basildon site has included £60 000 for a sophisticated cutting machine. The Divo 680-750 by Pro Saw has additional laser alignment and bundle clamps for cutting complete pipe bundles with pipe diameters of up to 8 in in one operation. This significantly impacts the throughput of material for both fabrication and stock holding back into our distribution network. Its speed of feed and cut time increases our capability to cut materials to specific lengths for spool manufacture or bag-and-tag Victaulic plant rooms.
![]() |
The outsourcing model also includes storage facilities, meaning that customers do not have to worry about incurring additional floor space and logistical costs. Our handling facilities are suited to managing projects with tube sizes of 30 to 700 mm bore.
There is no denying that building information modelling (BIM) is making an impact on the industry. I believe that we are not far off BIM controlling the construction process from start to finish. It could even take over the contract documents in a project to rationalise the workflow, reducing errors and waste.
In response to the progress of BIM, we have been training our CAD operators in a Revit drawing system for working towards full BIM compliance. This will provide an accurate representation of the actual plantroom building and equipment being used in the installation, enabling detailed modelling and piping installation. In turn this will ensure up-front accuracy in manufacture and installation as well as confidence in the supply and installation process.
As confidence grows in the benefits and use of BIM, it will become the standard, enabling detailed off site fabrication from plant room to utilities — significantly impacting shell and core fit-out times. This will help reduce building costs and enable more accurate pricing at the tender stage.
Metal fabrication is one of the key sectors that has suffered from a decline in skilled workers, especially in terms of the next generation. This was recently highlighted in the media, where it was reported that engineering in the UK had suffered a decline of 12.2% to 16 280 young people under 19 taking engineering-related advanced level apprenticeships in 2014.
It is essential to address this issue, as lack of talent will subsequently drive up associated product or service costs. While the country has a national incentive to drive apprenticeships in the manufacturing and engineering sectors, we want to ensure that we are maintaining the level of skill required to service our customers effectively. This takes the onus off the customer to invest in the required talent for the job.
For example, our teams have access to regular training programmes on systems such as BIM software, as well as being fully trained in the processes of express fitting and welding processes which are moving towards a more automated future. Overall, this level of staff development is resulting in an increase in the productivity and volume of work we are able to fulfil.
We embark on a constant programme of training and qualification, for example training our CAD team on Revit, detailed plastics training for pipe fitters for fusion welding and upgrading our welding techniques alongside our welding suppliers. Continuous product development with our project team ensures we meet customer demands technically and can consistently provide the optimum solution.
![]() |
Our team of engineers, pipe welding and fabrication experts, are qualified and coded to the highest industry standards. This offering of professional development has a positive impact on staff retention levels, which is demonstrated by the average number of years’ experience in the industry among our employees being 37 years.
The most obvious attraction to prefabrication is to speed up construction time, resulting in lower labour costs on-site. It can also allow for year-round construction, eliminating weather delays that might affect the site’s operation as well as reducing the threat of theft and vandalism. Furthermore, the mechanisation used in prefabricated construction ensures precise conformity to building code standards and greater quality assurance.
The holistic approach to metal fabrication presents a complete offering through partnership — working together to create a solution that best suits that business. We can take a whole tier-one contractor specification document, say 1900 pages, through to an A4 sketch from an engineer on site to look at the best solution for that specific project.
There are less wasted materials with pre-fabrication than in site-built construction because customers only pay for what is supplied. Put into perspective, the amount of material wasted on-site is generally about the same in volume as what has been installed, whereas pre-fabrication provides finished items in a timely manner. It is also limitless in size application, from a single 15 mm pipe run to a whole plant room or building service, small school boiler room to energy centre.
Another point is that protecting materials from exposure to the elements during construction reduces the risk of materials having to be replaced.
When asked why we have developed a new dedicated site in Basildon, the answer is simple.
We offer a fully-coded, fully-drawn weld-mapped service which is quality assured and backed by the support of an FTSE 100 company and country-wide distribution network. Additionally, we have a network of branches staffed by some of the most knowledgeable professionals in the sector where we can ensure the availability of associated products and components such as valves, boilers, heat interface units and loose ancillaries.
This one stop-shop approach essentially adds value to the work we carry out for customers so the business case should be easy to make. It is important for customers in this sector to consider adopting changing practices to remain ahead of the curve and demonstrate competitive advantage.
Gary Franklin is fabrication manager at Pipe Center’s recently opened fabrication facility in Basildon