Maintaining peak boiler efficiency
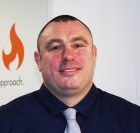
Stephen O’Neil of EOGB Energy Products looks at how significant efficiencies in heating systems can be delivered by optimising burner controls.
As the energy costs for environmental heating can represent a significant proportion of a building’s running cost, it is of paramount importance to maximise the energy and thermal efficiency of the heating system. This article examines some of the ways that existing installations can be improved to increase the overall efficiency of a building’s heating system.
The first step in ensuring optimum efficiency is to confirm that the burner is correctly matched to the boiler or heat exchanger. This will ensure that the burner can provide an optimum turndown ratio, thereby minimising burner cycling and ensuring that there are no excessive heat losses in the stack or undesired condensing if the burner is too small.
Combustion efficiency can be predicted by comparing the quantity of oxygen in the stack gases to that of theoretical or stoichiometric combustion conditions (assuming complete combustion). The lower the amount of oxygen (or excess air), the higher the combustion efficiency (Table 1).
Under normal operating conditions it is typical that the combustion engineer will set up the burner with a degree of excess air to ensure that it will not become starved of combustion air and cause incomplete combustion. Several factors can affect the combustion process over time.
Excess oxygen | Combustion efficiency |
2.0% | 83.08% |
2.5% | 82.37% |
3.0% | 81.68% |
3.5% | 80.71% |
4.0% | 79.72% |
4.5% | 78.60% |
5.0% | 77.31% |
5.5% | 75.32% |
6.0% | 74.03% |
6.5% | 72.01% |
• Barometric conditions Atmospheric temperature can affect the density of air and affect the fuel/air mixture. Altitude can also alter the quantity of oxygen within the combustion air.
• Calorific value The calorific value of a fuel can change from time to time and, as with the barometric conditions, affect the fuel/air ratio.
• Mechanical hysteresis Depending on the type of burner it can be possible for the burner settings to drift away from their original settings due to continuous operation.
It can be observed why it is necessary to introduce more air than that which is required for complete combustion, but this inevitably has an adverse effect on combustion efficiency.
While it is not cost effective to have constant monitoring by an engineer, it is possible to incorporate a constant monitoring system into the burner control.
O2 trim systems monitor the oxygen in the stack via a digital or analogue feedback system. They then adjust the burner air damper to the appropriate position to maintain a consistent quantity of O2 throughout the full operating range of the burner.
A good oxygen trim system will ‘learn’ during commissioning what the effect is to the burner for every single trim that it performs. This allows for full-time oxygen trim operation without the necessity of a full-time plant operator, irrespective of how plant conditions change, resulting in a significant improvement in burner efficiency.
![]() |
There are various ways of improving the efficiency of burners in existing heating installations. |
Although O2 trim technology can make significant savings if applied correctly, burner efficiency can be further improved with the introduction of CO (carbon monoxide) trim as well.
The COe sensor is identical to the O2 sensor apart from the fact that the electro-chemical and catalytic properties in the signal materials are different, thus enabling combustible components such as CO and hydrogen (H2) to be detected.
In the event of incomplete combustion, and in the presence of unburned hydrocarbons, a non-Nernst voltage forms on the COe (carbon monoxide equivalent) sensor. The characteristics for both sensors alter and relay a signal to the control module to adjust the burner as necessary. This process is identical if an excess of O2 in the atmosphere exists.
Close to the emission edge, the sensor signal for the COe electrode the ratio of unburnt hydrocarbons/ hydrogen increases at a disproportionate rate and searches for the optimum working point of the combustion, adjusting accordingly and optimising combustion further.
This procedure is repeated cyclically so that the optimum working points are always maintained, even for unstable barometric conditions, mechanical hysteresis or fluctuating calorific values.
The airflow of a typical burner is usually regulated by the graduation of an air shutter or damper via servomotors and cams. The fact that the fan is running at a constant speed inevitably incurs higher load losses, which in turn dissipates some of the electrical power generated by the fan motor.
![]() |
The incorporation of an inverter drive can vary the speed of the fan in correlation with the specific burner load, thus delivering energy savings (as well as reducing noise levels).The graph shows the energy savings on a Baltur 450 kW TBG burner by fitting an inverter drive to the fan motor.
By making various appliance modifications and adjustments, significant savings can be made — reducing running and maintenance costs as well as lowering carbon emissions.
However, as with any upgrade of existing systems, consideration must be given to the business case with regard to the financial implications for investing in such equipment with regard to the cost benefits to the business.
Stephen O’Neil is a technical specifications engineer with EOGB Energy Products.