The role of new technologies to improve heating commissioning
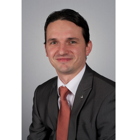
Errors and inconsistencies in the commissioning of boilers cost installers time and end-users money. More careful consideration of flow-rates and the adoption of new automatic commissioning technologies can change this, as Jonathan Grist of Viessmann explains.
Let’s get the bad news out of the way first. The efficiency and running costs of commercial heating systems can depend greatly not only upon the boilers specified but also how boilers are commissioned. Yet if you ask 10 different engineers about their commissioning methods, you’ll get 10 different answers.
One reason is that commissioning can be labour-intensive and time-consuming, so there is a temptation to cut corners. If we could speed-up the commissioning process at the same time as making it more consistent, installers and end-users would all benefit.
The good news is that this is possible. Part of the solution is to regard design as the first crucial step before commissioning commences. The other part of the solution is to take advantage of the technologies that can improve commissioning accuracy and reduce commissioning times.
Design is the essential first step.
There is no standardised method of commissioning. It might be argued that this wasn’t so important with old, floor-standing boilers, but that mindset is no longer adequate.
It is absolutely critical with modern boilers that commissioning and maintenance are carried out correctly. Manufacturers produce their own commissioning checklists (albeit with some variations) that should always be followed and can often be found online.
But here is the surprise; while engineers are listed with the Gas Safe Register to confirm they can work safely and legally on gas appliances, those responsible for what is really the first step in the commissioning process, the hydraulic system design, require no minimum standards or qualifications.
This means it is important to select a boiler not only for its technical specification and performance, but also for the manufacturer support that will accompany it. Choose a boiler manufacturer which will become involved in commissioning, to ensure that errors aren’t made, and which will remain involved afterwards to ensure efficiency is maintained. At Viessmann we believe this support is crucial to ensure the product performs at its highest level, not only from the outset but also over the long-term.
It is also worth contacting your boiler supplier to confirm who is responsible for what, as this isn’t always clear. For example, sometimes the new boiler will be added to an existing system with the use of a low-loss header; in this case the boiler manufacturer is responsible for the commissioning only up to the header.
Selecting your system designer is equally important. If the specification is wrong, the boiler will never be efficient. The boiler must be correctly specified for the system and flow rates. It’s essential to check that flow rates are perfect before commissioning and again when the system is fired. Put the boiler into a running model before commissioning, taking account of the system it’s attached to and how much water will go through it.
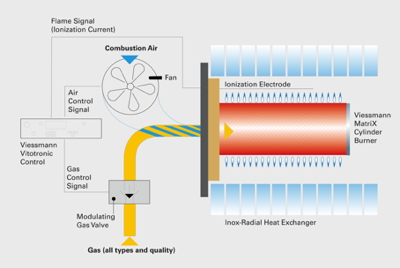
It is also crucial during set-up to achieve the optimum ∆T between flow and return. For example, the Viessmann Vitoflex 300 biomass boiler with a 15 K ∆T would require a flow rate of 17 m3/h. However, with a 20 K ∆T the same boiler’s requirement would be only 9 m3/h. Too high a flow rate could cause the boiler to cycle.
Choosing a boiler with inbuilt commissioning technology will automatically ensure correct settings.
Viessmann’s Lambda Pro combustion control technology, for example, automatically and independently controls the air and gas mixture through flame quality (ionization current). When the burner starts, the air flow is set to the start rate by controlling the fan speed. During the ignition period, the gas valves open and the gas flow rate is electronically set.
Eliminating the need for manual adjustment of gas valves speeds up commissioning and makes it failsafe.
After commissioning, Lambda Pro technology ensures permanent high operating efficiency. It achieves this by continuously adjusting the combustion to achieve constant CO2, even if there’s a change in the calorific value of the natural gas, liquefied natural gas, or liquefied petroleum gas fuelling the boiler. This means that one boiler is suitable for all gas types and altitudes, with no conversion required.
Also important are laptop software commissioning tools. An example is Viessmann’s Vitosoft 300 software module for servicing, commissioning and diagnosis of heating systems. A laptop carrying this software can be plugged directly into the boiler, assisting with the all-important hydraulic set-up and making commissioning quicker and easier.
So the bad news with which we started this article need no longer apply. With the right technology, commissioning can be consistent, engineers can avoid errors and save time on-site, and end-users can benefit from a heating system running at optimum efficiency and performance.
Jonathan Grist is commercial sales director with Viessmann.