CHP — a long-term relationship
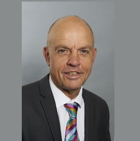
As electricity prices continue to rise, the case for combined heat and power (CHP) grows stronger. However, the benefits of CHP can only be realised if systems are designed, installed and commissioned and monitored correctly. Gary Stoddart of Remeha CHP advises businesses on best practice before, during and after the installation of a CHP unit.
In line with forecasts, the gap between electricity prices and gas prices — often referred to as the spark gap — continues to widen. According to the latest report from the Department for Business, Energy & Industrial Strategy (BEIS), the price of gas for non-domestic customers fell slightly between Q2 and Q3 last year, while electricity experienced an increase. The average cost per kWh for electricity was 10.39 p while gas was 2.37 pence (Ref. 1).
In line with forecasts, the gap between electricity prices and gas prices — often referred to as the spark gap — continues to widen. According to the latest report from the Department for Business, Energy & Industrial Strategy (BEIS), the price of gas for non-domestic customers fell slightly between Q2 and Q3 last year, while electricity experienced an increase. The average cost per kWh for electricity was 10.39 p while gas was 2.37 pence (Ref. 1).
For businesses concerned about the effect of this disparity on their energy bills, implementing a CHP system could be the answer. CHP systems burn natural gas to generate heat, while also providing electricity to supplement or replace the grid supply. Generating electricity on site can reduce energy bills by around 20% compared to conventional power generation (Ref. 2).
By using a CHP system, businesses can produce electricity at gas prices, which is cheaper than buying it directly from the grid, as electricity is approximately 8 p more expensive per kWh. Also, in comparison to purchasing from the grid, CHP electricity doesn’t suffer transmission losses caused by moving power over large distances, resulting in a more efficient process.
Furthermore, by generating heat and power simultaneously, CHP can reduce carbon emissions by up to 30% compared to conventional methods (Ref. 2). At the same time, where heat from the generation process is lost at gas-fired power stations, the heat generated by CHP can be re-used in the heating/hot water systems.
For these savings to be achieved, however, the CHP unit must be appropriate to the needs of the building and its users, be specified and installed correctly, and be used as intended. Sadly, incorrect specification is all too common, leaving many building owners disappointed with the performance of their equipment.
One reason for this disappointment is the age-old ‘10%-for-luck’ rule, which means that buildings are given larger plant than they actually need. This means that not only is the initial capital outlay of the equipment more expensive, but also it will not run efficiently, leading to higher operating costs. Oversized CHP units will not run if the heat demand is not present, and as a result electricity will not be generated.
The golden rule for CHP is to keep it as small as possible and to remember that properties with high and continuous, year-round heating loads, such as hospitals, hotels and leisure centres, achieve the most efficient operation. Sizing the system so that the base-load heating requirements can be met largely by the CHP unit alone will result in the continuous generation of low-cost, low-carbon electricity as a by-product of producing base-load heating.
When calculating the size of the system, Building Regulations state that CHP must be sized to provide ‘not less than 45% of the annual total heating demand’, which includes space heating and domestic hot water. This is critical for CHP as oversizing for summertime loads can result in either non-operation of the CHP or the heat produced being ‘dumped’ in order to continue generating electricity.
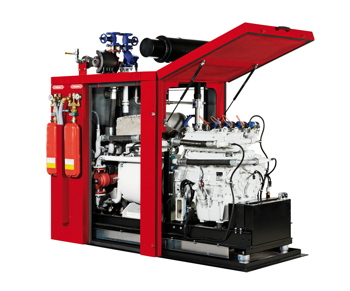
Thermal storage is often the best way to keep CHP running 24/7, especially if a site has peak demands for hot water. The heat produced by the CHP unit over a 10-hour-plus period can be stored in a preheat cylinder, and the hot water can then be used over a peak period (6.30 to 9 am, for example). The cylinder is then charged again throughout the day, ready for the evening peak period (say 4.30 to 7pm). If the peak periods are greater than this, the storage capacity can be reduced.
A CHP unit supplements existing boilers and/or water heaters, so in a properly designed and commissioned system, the heating and hot-water equipment within the building will draw on the storage first, before demanding additional supply from the boilers. This ensures that the building gets maximum output from the CHP, which replenishes the storage, and the boilers only run for the shortest possible time during periods of high demand for hot water, reducing gas consumption and carbon emissions as well as extending their operating life. This is easily achieved with CHP if the system is sized and integrated correctly; at Remeha we assist with system design to ensure that storage vessels are correctly sized and adequate heat is provided for peak usage times.
While correct sizing and system design are critical, consideration should also be given to the availability of a suitable, long-term maintenance contract. This way, the CHP supplier can monitor the system to ensure it continues to perform at the optimum level.
Having said this, there are currently a large number of CHP units installed across the country that are not running as intended — something which could be easily rectified through early discussions about system design and effective, ongoing monitoring.
A modem, connected to a landline or mobile network, can transmit data between the site and the CHP unit’s monitoring centre. The manufacturer will have the resource and expertise to analyse data in real time, and can provide guidance on how to solve any issues or alter the system to maximise performance, efficiency and cost savings. Knowing about any anomalies early can save the end user from significant losses due to unplanned system shutdowns, maintenance and repair. What’s more, if the CHP unit is being remotely monitored through a modem, it will also inform the end user and the service team when a service is due.
With the ‘spark gap’ showing no sign of narrowing, CHP provides a welcome antidote. By working closely with technology providers to design, commission and run CHP systems in the most effective manner, businesses can realise incredible savings on their energy bills and carbon emissions.
Gary Stoddart is technical sales director with Remeha CHP.