Considered connections
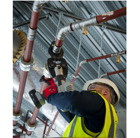
Speed is of the essence when it comes to pipe fitting in today’s large-scale projects. Scott James offers his advice on making the right choice.
With tight project deadlines, measures that optimise speed of installation and minimise delays can prove invaluable. And when it comes to pipework installation, press connection technology can offer just that.
Compared to soldering, press connections provide a significant time saving. This is particularly valuable on large projects where the size and complexity of the pipework system could require hundreds or even thousands of connections.
The process requires minimal preparation. Installers simply need to cut the pipe to size; deburr the cut surface; slide the fitting onto the pipe and press the connection. There is also no need to clean the surface of the pipe to remove excess materials once the joint has been made.
For certain applications, especially public sector organisations such as healthcare and educational facilities, heavyweight steel tube is frequently the preferred material. In these situations the advantage that press connections have is even greater, with potential time savings of around 60% compared with threading. For large diameter pipe of up to 4 inches, where welding is the conventional approach, the reduction in assembly time can be as much as 80%.
Furthermore with no hot works, solder, chemicals or oil used in the installation process, press connections are safer and cleaner - significantly reducing the risk of fire and contamination.
When specifying pipework for any system, one of the most important considerations is to ensure that joints are robust and reliable.
This consistency of the seal is a key advantage of press connection technology – especially where multiple operatives will be working across the site. However, a poor quality product that does not create a strong connection can prove costly in the long term. Systems that feature a double press profile in the design of the fitting – both before and after the sealing element create a permanent connection that resists both longitudinal and torsional forces. This will ensure that any work carried out around the pipework during installation and throughout the life of the building will not affect the connection.
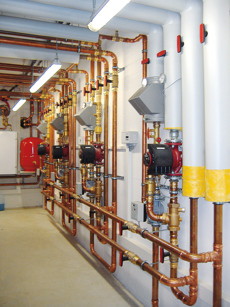
Furthermore, ensuring that the product is suitable for the intended purpose is essential. The material used in the sealing element within the fitting must be able to withstand the temperatures and substances it will be exposed to. For example, EPDM (ethylene propylene diene monomer) is primarily used for drinking water and heating installations, HNBR (hydrated acrylonitrile-butadiene rubber) for gas, heating oil and diesel pipes and FKM (fluoroelastomer) for higher temperature range applications. Manufacturers will often have a range of products specifically designed with the appropriate level of chemical or temperature resistance.
Another key consideration is detecting any leaks in the system following installation Press connections offer an advantage here too as the joint is either pressed and strong permanent seal has been created or unpressed entirely. However, it is important to select a system that will allow clear identification of these unpressed joints. Without such a feature, fittings that may have been inadvertently unpressed during installation may not leak at testing pressures but will fail when the system is in use.
There is also the issue of contamination to consider. While the most obvious part of this is selecting products that do not include materials that would contaminate the water, bacterial contamination is also a concern. For this reason products that have been dry tested should be favoured. Once bacteria are established in the system it can be difficult to remove.
Finally, the choice of press connections also has an effect on the performance of the system. The fittings, pipe and design of the pipework all contribute to the friction in the pipework and reduce the flow velocity. Not only can users of the building experience low water pressure but there is also increased risk of backflow from equipment on the system that creates a higher pressure.
The benefits of press connections for large scale projects are increasingly being recognised, however as with all components that go into building systems, selecting correct, high quality solutions that are fit for purpose is vital. This ensures simple, issue free installation and commissioning as well as the long-term durability of the system.
Scott James is director at Viega