Going offsite
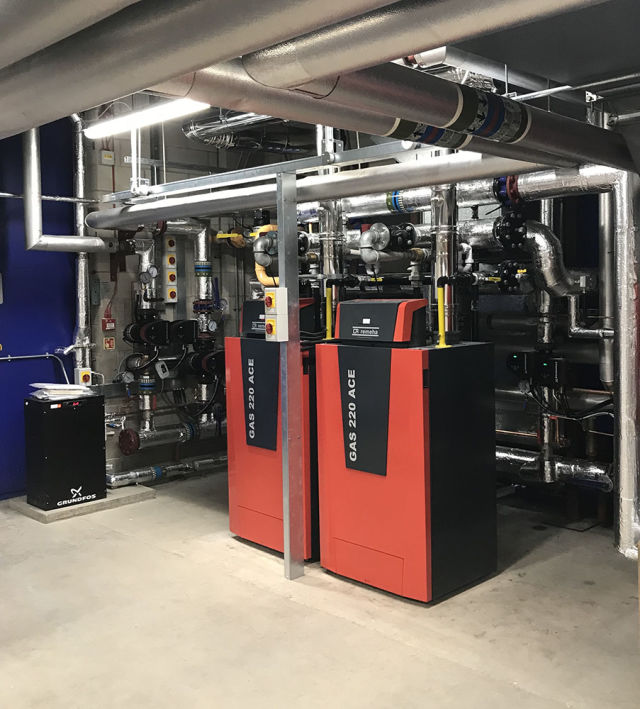
Offsite fabricated heating techniques offer numerous benefits that can help resolve common refurbishment challenges, says Paul Arnold.
For some time, energy efficiency has been considered as one of the long-term ‘quick wins’ to boost building performance and meet environmental targets, with heating as a frequent starting point for improvement. But while good quality installation is key to achieving long-term efficient building performance, as engineers know only too well, it’s often carried out in challenging circumstances.
Tight project schedules, typically compounded by plant room space constraints, and access restrictions, can complicate what can and should be a straightforward boiler replacement. Offsite manufacturing is one way to overcome these hurdles and it is well established in the building services industry as a technique that can deliver quality, customisation and cost benefits with reduced waste. And when it comes to heating, adopting a similar approach through prefabrication can deliver all these advantages and more.
It works by taking offsite fabricated cascade arrangements which are designed to simplify multiple boiler installation. Each module can be designed using BIM tools and 3D computer-aided design (CAD) systems. The early visualisation enables the consultants, contractors, offsite manufacturers and clients to collaborate on the system design and evaluate the functionality before any work takes place.
In this way, it ensures a robust design that factors in the unique requirements of the project and site from the outset, reducing the risk of project delays. The result is reduced on-site time and labour, improved on-site safety, and zero to minimal disruption. And as the bespoke units are produced under factory conditions, there is the added bonus of factory quality assurance and pre-release testing.
This approach is being used as part of a recent major heating refurbishment programme carried out for Nottinghamshire Police at seven of its police stations.
A condition survey of the mechanical installation by project consultants CJR Midlands (CJR) across the sites found that there were severe failings in most of the existing aged plant. As a result, Nottinghamshire Police were keen to install a more efficient, long-term high-performance heating system that would reduce energy use and minimise associated costs and emissions while improving comfort levels for their staff at the same time.
The key requirement was that all the police stations should remain operational throughout the upgrade. This meant ensuring that there would be zero disruption to the hot water service during the works, and that all systems would be fully operational by the start of the new heating system.
The critical challenge on this project was the tight schedule, as all sites needed to be fully completed within three months, before the start of the heating season.
To meet the requirement for improved efficiency, CJR recommended refurbishing the seven plant rooms with high efficiency condensing boilers together with associated pumps and flue vertical masts. New building controls were also specified to enable CJR to monitor all the sites from Sherwood Lodge, the main police headquarters, for improved energy management.
Due to the age of the heating systems, the decision was also taken to apply a plate heat exchanger (PHE) to achieve hydraulic separation between the boiler circuit and the heating circuit, and so optimise boiler performance and longevity.
At six of the sites, CJR specified a combination of Gas 220 Ace floor-standing boilers with offsite fabricated cascade arrangements to achieve the required heat output and heating reliability and efficiency within the time constraints. At Radford Road police station, two Remeha Gas 310 Eco Pro condensing boilers were specified to meet the site requirements.
When it came to boiler specification optimising heating efficiency and reliability throughout the boilers’ lifecycle is an influencing factor.
David Griffiths, regional director at CJR, says that the boiler manufacturer was a consideration: “Working within such a narrow timeframe, it was essential to select a proven manufacturer so we chose Remeha. They have consistently provided us with excellent service and support, including assisting with surveys. The good availability of spare parts was also key.”
ABSN were the M&E contractors on the refurbishment programme for the main contractors GF Tomlinson. The design was based on 3D drawings of the boiler cascade arrangement to the specified layout for each of the six sites. Low temperature hot water (LTHW) and gas headers, pump sets and a PHE were integrated into the design.
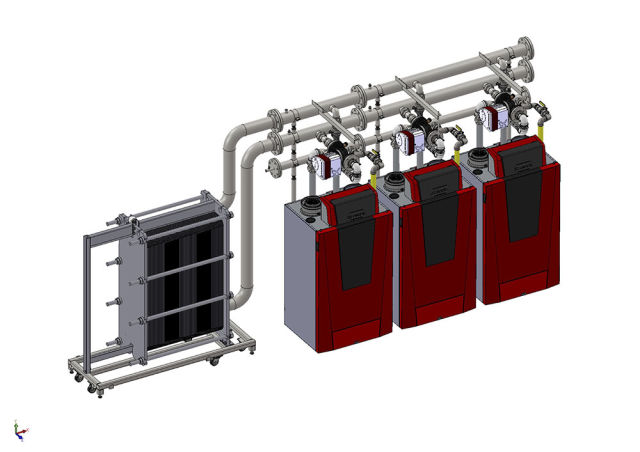
The drawings provided early visualisation of the layout before the offsite production took place. Griffiths adds that design was important: “As we also design in 3D, the fact that the drawings were available in the same format enabled more close and accurate design.”
A major advantage of using offsite fabrication was the ability to prepare the connecting pipework before delivery of the boiler modules.
ABSN contracts director Nick Clews says there were methods to speed up the process: “Having the detailed, co-ordinated dimensioned designs for each plantroom allowed us both to procure and to preinstall pipework in readiness for the boiler delivery. This helped speed up the installation process considerably.”
Production of the boiler modules was carried out in a quality-controlled factory environment, with end-of-line testing providing assurance that the specification was met. The boilers were then delivered to site on a wheeled unit for rapid positioning, connection and commissioning.
The ability to achieve the physical design of the cascade system ahead of delivery was a key specialist contribution that helped to ensure successful project delivery. The refurbishment scheme went smoothly, with the heating system brought online in a short period of time and the challenging delivery dates all met.
Crucially, for Nottinghamshire Police, this offsite approach delivered on all fronts, providing a rapid, high quality solution to improved heating efficiency at all its stations.
“The project went extremely well,” observes Griffiths. “Since monitoring the sites, there have been no issues with the Remeha boilers.” Griffiths adds that others were satisfied with the project: “Nottinghamshire Police are also pleased with the end result, especially as the collaborative delivery enabled the team to deliver on time and on budget.”
The plant room refurbishment illustrate that applying offsite fabricated heating solutions can deliver benefits at every stage of the project - from design and specification to installation, commissioning and future maintenance. And as the cost, size and specification are all fixed and in place, this helps keep the project on time and on budget.
For the end-user, the result is high performance heating and minimal on-site disruption. For consultant engineers, the improved design flexibility makes it easier to meet all project and customer requirements.
The contractors are able to plan ahead more accurately, putting high-intensity skills to use on other projects. Hot works are also reduced, creating a safer environment for installers and end-users.
With clear advantages for the entire supply chain from prefabrication techniques, going offsite has the potential to make everyone a winner.
Paul Arnold is Remeha product manager