Efficient Air Control for University Laboratories
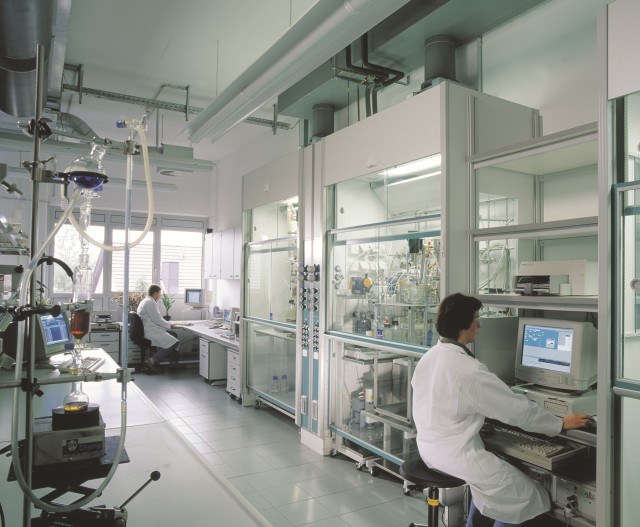
Laboratory buildings can be responsible for 50-80% of non-residential carbon emissions at research-intensive universities. Ian Thomas, Product Manager for Labcontrol at Trox, looks at the issues.
Recent events have highlighted the crucial role played by university laboratories across the UK. In addition to training the next generation of scientists and clinicians, the science campus is essential if the university is to carry out the internationally-recognised research on which its reputation depends.
For those concerned with university finances or sustainability, however, the science campus involves a significant overhead. The energy consumption of university laboratories is often more than three or four times that of ordinary teaching spaces on a square metre basis[1]. This can mean that laboratory buildings are responsible for between 50% and 80% of the total energy-related (non-residential) carbon emissions of research-intensive universities.
The higher energy costs and carbon emissions of the science campus are typically associated with the need for specialist air supply and extraction to ensure that laboratory operations can be carried out safely. Chief among these is the usage of conditioned air for fume cupboards. When sashes of fume cupboards are open, the volumes of air required to maintain a safe working environment for laboratory personnel increase significantly. For example, a 900mm wide cupboard with a maximum sash height of 500mm and face velocity of 0.5 m/s would extract approximately 225 l/s of conditioned air from the room.
When attempting to reduce energy consumption of the university science block, the health and safety of students and staff is obviously paramount. There are a number of ways, however, in which air supply and extraction can be managed more effectively, to reduce the science campus’s environmental footprint and financial overhead whilst safeguarding lab occupants at all times. This article suggests a few proven approaches.
First steps
Across the UK as a whole, the equipment currently installed in university science facilities varies significantly in terms of age and functionality. So an immediate priority is to ensure that any constant volume fume cupboards that may still be in operation on the campus are upgraded or replaced to facilitate operation with variable air volumes.
As already mentioned, a 900mm wide cupboard with a maximum sash height of 500mm and face velocity of 0.5 m/s would extract approximately 225 l/s of conditioned air from the room. This would be fixed on a constant volume cupboard, whereas on a variable volume cupboard the minimum air volume could be around 55 l/s when the sash is down. So converting from constant volume to variable volume would therefore save 170 l/s when the sash is in the down position for a single cupboard. If a university is currently operating with a number of constant volume fume cupboards, just a simple upgrade to variable volume could make a significant improvement.
Another immediate priority is to tackle unnecessary wastage of energy relating to day-to-day use of the equipment. It is common, for example, for the sashes of fume cupboards to be left open at times when students or researchers are away from the equipment. Reductions in energy consumption can often, therefore, be achieved by working with the university to determine ways in which the wastage of air can be reduced by good laboratory practice. This could involve encouraging students to close fume cupboard sashes whenever the work stations are unattended. Alternatively, auto-close mechanisms can be fitted to fume cupboards to ensure that sashes close automatically, if left open unnecessarily.
Room air management
Simply installing variable volume cupboards may not be sufficient to achieve the university’s ambitious sustainability targets however. The increasing visibility of energy efficiency data of universities, and the growing importance placed on sustainability by government, management teams, and students themselves, has brought environmental performance to the top of the agenda. People & Planet’s University League table, for example (now in its tenth year) creates an alternative merit roster for higher education sites, rating them from ‘first class’ for their sustainability, right down to a fail. With such transparency, the environmentally-conscious university typically has a clearly-defined strategy to achieve significant reductions in energy consumption over time.
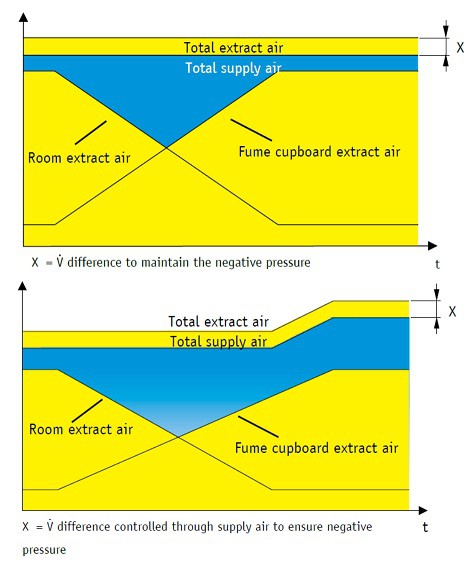
An effective option to reduce the environmental overhead of the science campus without impacting on its teaching and research capabilities is to integrate fume cupboard air supply and extraction with the wider air management systems. Installing a room air management system makes it possible for all input and extract air for the laboratory to be controlled automatically to ensure that the required ventilation strategy and levels of safety are maintained. With this design approach, the supply and extraction of the fume cupboards (or other technical air management devices) is automatically balanced and offset in line with changing requirements, reducing the total supply and extract volumes. For example, if the fume cupboards are open and extracting air, there is not the same requirement for the room system to carry out this process. By scaling down room exhaust air extraction in line with fume cupboard extraction, the room air management system is able to prevent over-supply and extraction of conditioned air from the space, improving energy efficiency significantly (see Figures 1 and 2).
Working smarter
Another benefit of a well-designed air management scheme for the science campus is the ability to reduce expensive periods of under-occupation of the laboratory facilities by enabling multiple scientific disciplines to work safely alongside one another.
At the University of Birmingham’s new Collaborative Teaching Laboratory (CTL), for example, the installation of advanced air management technology is providing the flexibility necessary to maximise occupancy levels. In one area of the CTL, for example, the air management system, integrated with the site’s BMS, optimises energy efficiency of 50 fume cupboards. It divides the lab into 5 zones, each with 10 fume cupboards, fitted with fume cupboard controllers. Sash distance sensors control the volume flow rates based on the height of the sashes, and user displays, with traffic light warning systems and audible alarms, contribute to safe working procedures.
Each zone features two supply air VAV units which track the extract air, ensuring the maintenance of correct leakage flows. By matching the supply of air to the changing requirements of the space these features reduce over-supply and wastage of conditioned air, ensuring that multiple scientific disciplines can carry out teaching and research safely side-by-side, whilst achieving the optimum level of environmental and financial performance. The resulting levels of efficiency have contributed to the building’s ‘Excellent’ BREEAM rating.
At the University of Wolverhampton, a number of energy-saving opportunities were adopted when designing the new Rosalind Franklin Science Building. A TROX EASYLAB room air management system has been installed to manage the supply and extract controllers for over 50 fume cupboards. Responding rapidly to changes in extract volumes by the technical extraction devices, the room air management system offsets one form of exhaust air against another. This maintains the correct air flow balance and room pressure at all times in the laboratories, whilst generating energy savings by preventing over-supply and extraction of conditioned air. Auto-close mechanisms fitted to fume cupboards ensure that sashes close automatically, if left open unnecessarily, and integration with the university’s BMS means that air change rates can be reduced, without impacting safety, at times such as weekends and evenings, when the laboratories are unoccupied.
Moving forwards, the importance of laboratory facilities in universities, hospitals, government sites and private companies has become all too clear.
[1] Peter James and Lisa Hopkinson, ‘Carbon, Energy and Environmental Issues Affecting Laboratories in Higher Education - A Supplement to the HEEPI Report on General Regulations and Schemes on the Topic’, August 2011.