Corrosion damages pipework and reputations

Steve Munn, MD for Hevasure, explains the negative effect of corrosion on sustainability and how to combat this scourge of closed-circuit systems
Modern building services need to be energy efficient, sustainable and long lasting with specifiers taking great care to create optimum designs to minimise environmental impact and reduce running costs. What is often overlooked, however, is how water-based HVAC systems will stand the test of time, specifically the threat caused by corrosion
Closed circuit water systems are prone to corrosion, an age-old problem that threatens to compromise the most well-designed HVAC schemes. Keeping it out of a system begins with good design and installation practices and ends with a life-long commitment to checking the parameters that could lead to corrosive conditions.
In the past, whole-life sustainability and costing was possibly not the priority. Specifiers were concerned with creating a scheme that performed well on paper. M&E contractors put this scheme together as directed and once handed over, it was no longer the problem of the parties involved throughout these initial stages. In a world where reducing carbon footprints is key, a short-term view is not responsible. However, and when reputations are at stake, the best in our business should want to create HVAC systems that meet the design parameters set out for them, both long-term and short-term.
Corrosion causes problems
Corrosion significantly impacts the performance of water reliant piped services in a number of ways:
- Build-up of debris in pipes and components causes restriction, which can lead to increased pump energies in order to maintain flow rates.
- Heat transfer is reduced as a result of corrosion debris on heat exchangers and emitters.
- Valve seats can be eroded, leading to changes in flow characteristics.
- Heavily degraded pipework and components will eventually leak.
All of these issues will lead to reduced efficiencies, expensive repairs and ultimately breakdown. When a system breaks down, the costs in large commercial buildings can run into the millions. During repairs downtime is likely, which can cause lost revenues for the organisations on site. In mission critical locations, such as data centres, unplanned downtime is the ultimate nightmare scenario.
The main cause of corrosion is oxygen ingress. Keeping it out of a closed system must begin from the moment the pipework and component material is chosen and installed, and continue throughout its working life.
Most metals can corrode
Thin-walled carbon steel is a popular choice with today’s specifiers, but can cause trepidation because it is prone to corrosion damage and pin-holing. Light-weight and easy to install, carbon steel has much to recommend it. If you prevent corrosion from happening in the first place then there really is no issue.
A thicker walled, mild steel, commonly used in older systems and for components such as pumps, might seem like a safer option. Corrosion still happens, it’s just that wall penetration is less of an issue due to the thickness. In closed circuit systems plumbed with mild steel, corrosion debris can be transferred round the system causing blockages and efficiency losses. This debris can also settle where flow rates are low, creating the right conditions for bacterial proliferation and localized pitting.
Even metals that are normally passivated can corrode if conditions in the water change. Aluminium loses passivation if the pH rises above 8.5 and stainless steel doesn’t fare well in chlorinated waters. It’s important not to forget the components too. Valves are often made of brass, for example, which will corrode in ammoniacal or aerated water.
Prevention is key
So how can corrosion be prevented?
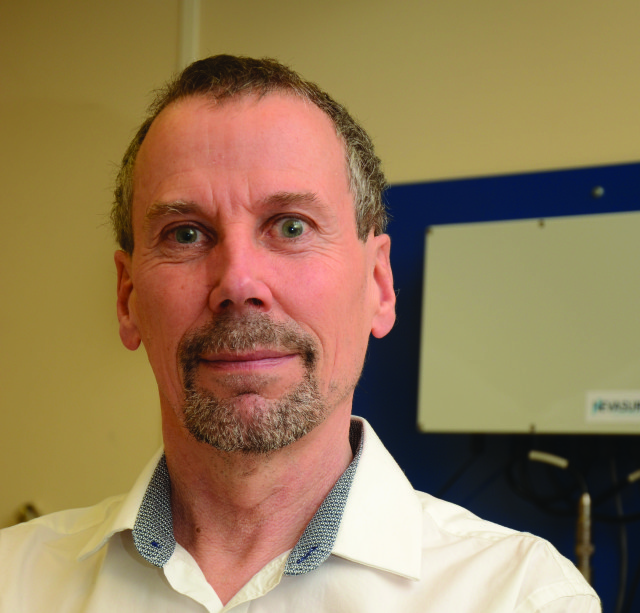
As touched upon, stopping oxygen ingress is key. Detecting its presence using real-time remote monitoring, along with the parameters that cause it to enter systems, such as pressure or make-up water flows, is critical. Measuring other contributory factors, pH, inhibitor levels and temperature, provides a full picture allowing issues to be acted upon and hopefully solved.
Until the advent of remote monitoring the only means of checking for corrosive conditions was sampling, a process which tends to focus on the wrong things and under report other significant parameters:
- Debris such as iron or copper oxides can be missed if they adhere to the walls of pipes and components
- Bacteria levels, although important, are not necessarily indicative of a problem if planktonic and not forming colonies under corrosion debris or biofilms
- Dissolved oxygen is not measured
- The causes of aeration, including pressure changes and fresh make-up water, are not detected
The other issue with sampling is that it can take many days for the results to return, by which time conditions may have changed.
Remote monitoring really is the only solution that accurately checks condition at all stages of a closed-circuit water system’s life. It allows everyone involved to be confident that they are passing on and then maintaining a system that will be as efficient and long-lasting as its designer intended. In fact, this new technology’s impact is now making its way into the very guides that ensure high standards in building services.
Industry standard
The 2020 edition of BG29 (Pre- commission Cleaning of Pipework Systems) has been updated with an emphasis on remote corrosion monitoring, a solution that has been making a significant impact on water system construction and management in recent years.
By effectively detecting adverse conditions, corrosion can be stopped before it even starts. This is crucial at the pre-commission cleaning stage, essential at handover and key to whole life sustainability and costings.
Building owners should be demanding this technology, especially when you compare it to the alternative.
Design for life
Wherever you sit within the building services food chain, if you care about your customer, the environment, your reputation then really understanding what’s going on in a close- circuit system is the only way that performance and efficiency will be delivered at every stage.
Details of Hevasure’s remote monitoring technology can be found at www.hevasure.com