The Future of Heat

The way we heat UK buildings will need to change significantly if we are to achieve our 2050 net zero goal. What could the future look like for the UK’s commercial buildings? Tom Murray of Baxi looks at the options.
In 2019, the UK government passed legislation requiring the UK to reach net zero status by 2050.
Since then, huge progress has been made in reducing greenhouse gas emissions, largely due to the reduction in the use of coal-generated electricity. But while the nation is on track to meet our 3rd carbon budget (2018 – 22), more needs to be done to meet our 4th (2023-27) and 5th (2028-32) budgets. As around 37% of UK emissions come from heating and hot water in buildings, the near complete decarbonisation of heat is required to achieve the challenging target.
The focus to date has largely centred on the UK’s circa 28million existing homes. But given that non-domestic buildings are responsible for 17% of UK energy consumption and 12% of greenhouse gas emissions, they too will play an essential role in hitting net zero.
As the building services industry is only too aware, there is no single ‘silver bullet’ solution to the urgent heat decarbonisation challenge as each building will have its own unique requirements. Instead, applying a mix of technologies and approaches, each appropriate for different applications, will offer a combined solution to the challenge ahead. These are likely to include electrification, decarbonisation of the gas grid and heat networks.
Electrification & heat pumps
Let’s start with electrification. In the last ten years or so, the UK has seen a dramatic decarbonisation of the electricity grid, thanks to large levels of investment in offshore wind farms. It therefore makes environmental sense to switch to low carbon electric heating technologies such as heat pumps in new build and off-grid developments.
The merits of applying heat pumps in well-insulated buildings are well established. We see Air Source Heat Pumps (ASHP) as the most popular and cost-effective choice of heat pump and will soon be offering them as part of our wide portfolio of commercial heating and hot water solutions.
However, retrofitting heat pumps onto older heating systems in leakier buildings is not always so straightforward. One reason is that older systems tend to run on high flow and return temperatures (typically 82ºC/71ºC) while heat pumps will typically optimise their efficiency at low flow temperatures (around 30-55ºC). This means that the existing system design will need to be addressed if the required heat pump performance is to be achieved.
Additionally, only a small portion of ASHPs can generate temperatures high enough to store domestic hot water above legionella temperatures (60ºC or higher). Therefore, until heat pump technology evolves, adding a hot water store could well be necessary in older buildings to achieve the higher temperatures.
Other factors for consideration are the energy efficiency measures that will need to be carried out in inefficient building stock to improve the fabric of the building and the likely need to increase the electricity supply into the building. All of this has financial implications. As more than 80% of today’s UK buildings are expected still to be in use by 2050, we must therefore assume that many types of structures will need further financial support before they can transition from gas boilers.
Further practical aspects to consider on retrofit projects are space planning to accommodate ASHP units and the noise factor, which tends to escalate during periods of high demand.
And while the electricity grid is evolving fast, the higher peak loads imposed by the uptake of electric vehicles will add to overall load on the electricity grid and generation capacity. The reality is that at present, in winter months, where the grid will experience peak heat demand, the systemic constraints with electricity generation capacity and distribution will make a complete switch to full electrification both extremely challenging and impractical for heat and transport.
Hydrogen
So what alternative options are there to achieve low carbon heat in the UK’s existing building stock?
Given that 85% of UK buildings are connected to the UK’s extensive gas grid, one low disruption solution is to repurpose the gas grid to transport green gas.
As hydrogen is a gas, it can capitalise on existing infrastructure while transitioning us to a cleaner fuel source. Using the hydrogen gas resource for heat also means that the valuable renewable electricity produced from sources like wind and solar can be put to full use in summer months to help generate green hydrogen, making use of the asset capacity even during periods of low demand, thereby offering interseasonal storage.
Although local network conversion to ‘pure’ hydrogen is unlikely to happen until around 2030, there is a push for ‘hydrogen ready’ boilers to be mandated to speed up and facilitate a faster change-over.
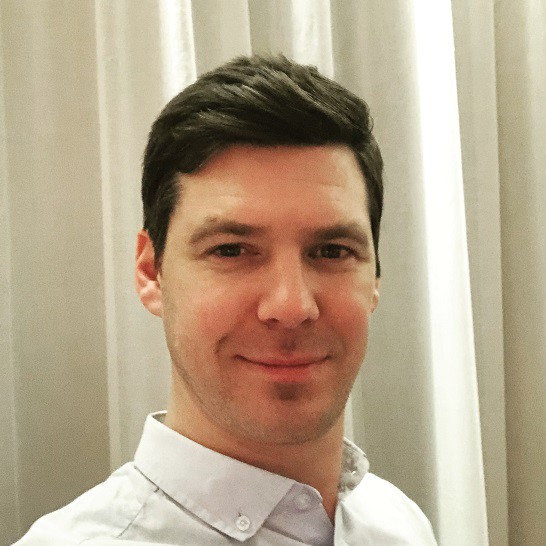
This will allow a boiler that works on natural gas when installed to be converted quickly and simply at the point of a local gas network changeover. As such, it offers a solution to low carbon heat in retrofit applications at a far lower level of disruption than alternative options.
How far down the line is hydrogen? Working with UK government and key industry stakeholders, we at Baxi Heating are actively working to establish the feasibility of replacing natural gas with hydrogen in residential and commercial buildings. 20% hydrogen blends are being demonstrated using current boilers at the HyDeploy project at Keele University.
The next step could be to convert the gas network to deliver pure hydrogen, meaning zero carbon at point of use. We are demonstrating prototypes of 100% hydrogen boilers through the UK government Hy4Heat programme with larger scale trial projects in development.
While demonstration and feasibility work continue, it isn’t possible to give firm dates for change. But it’s not far-fetched to envisage businesses and organisations in existing buildings running on low carbon hydrogen long before 2050.
Immediate solutions
But what about the immediate term? Given that many commercial buildings rely on natural gas for heat – and are likely to continue to do so for the next decade – the priority must be to use this energy source as efficiently and effectively as possible.
It’s therefore vital not to neglect the practical, affordable opportunities to avoid energy waste and cut consumption and emissions associated with heat in these buildings.
Replacing any old or inefficient heating plant with more efficient condensing boiler technology, for example, is a highly cost-effective and pragmatic starting point towards more energy efficient heating. As such, it will help us make considerable strides towards a low carbon future.
Heat networks
The final strand of the net zero pathway is heat networks. In dense urban environments, including multi-occupancy developments, heat networks will play an increasingly important role in the sustainable heating policies mix – with the government aiming to increase heat demand from heat networks from 2% to 18% by 2050.
Heat networks, which use heat efficiently close to the point of generation, can use a range of heat generation solutions. We see a clear role for ASHPs but also for natural gas or even hydrogen Combined Heat and Power (CHP), working in conjunction with hydrogen boilers and/or heat interface units.
When designing heat networks, we should also consider applying complementing methods of heat generation, for example using hydrogen boilers and CHP units to provide high grade heat for domestic hot water while powering ASHPs for low grade heat.
Challenges and opportunities
While we await definitive government guidance on the future energy mix and decarbonisation pathway, forward-thinking manufacturers are busy innovating to provide the necessary technologies and techniques that will drive full decarbonisation of heat in non-domestic buildings.
And as we continue to evolve these technologies and their applications, we look forward to supporting contractors, designers, consultants and building end-users on the UK’s journey to net zero.
Tom Murray is Commercial and Residential Specification Manager at Baxi