Grooved systems optimise mechanical room efficiency
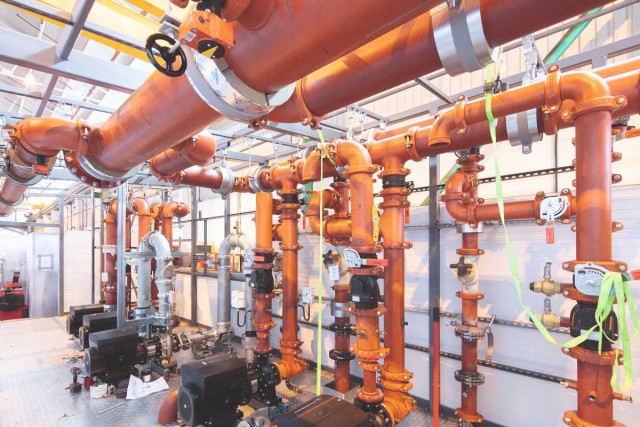
Grooved-end mechanical piping systems reduce the mechanical room footprint, enhance system performance and save time and cost on installation, says Shaun Hughes of Victaulic.
Controlling costs and compressing schedules without sacrificing quality are key concerns for contractors responsible for mechanical room installations. Alongside these drivers, space is becoming a critical factor. The high cost of commercial and industrial building space and its scarcity has also led to a growing trend to squeeze the size of mechanical rooms.
Grooved-end mechanical piping systems address all these issues. The lighter weight, smaller size yet higher integral strength of grooved components compared with welded or flanged systems, make them ideal for projects that are tight on space or where mechanical rooms are located on higher-level floors. Their ease and speed of installation offer savings on total installed costs and they also deliver improved performance and reliability.
Eliminating rubber bellows
In traditional mechanical room set-ups, rubber bellows or compensators are placed in the piping system at either side of the pump to reduce noise and vibration, and are sometimes used to correct misalignment between welded pipe and equipment, placing the rubber under intense stress in a certain plane. Not only do they take up valuable plantroom space, but rubber bellows are considered the weakest point of an installation and the first component that is likely to fail, as general wear and tear, along with exposure to UV light in the mechanical room, causes the rubber to erode.
Installing three grooved flexible couplings on each side of a pump solves these problems. It eliminates the need for costly, bulky flanged units and avoids the use of rubber bellows. The coupling construction enables the gasket to seal against the pipe, while the metal housing provides both space for the resilient elastomeric material to flex, and containment to prevent overstretching. This creates a discontinuity similar to that of a rubber compensator. Additionally, ductile iron and stainless steel both have their own vibration dampening qualities, so the external housing also serves to absorb sound, thereby protecting equipment and enhancing the lifetime of the system.
Three flexible couplings can be used not only with pumps but also with chiller units, cooling towers and any equipment with an engine that causes vibration. The use of additional grooved couplings - whether flexible or rigid - in the distribution lines will further reduce the transmission of vibration. By combining versatility with durability, the method provides a low-maintenance solution that saves space and delivers both practical and commercial benefits throughout the life of the system.
Improving pump efficiency
Cavitation is a problem frequently experienced, especially where space is limited.
When turbulent water enters a pump chamber and the suction eye of a pump impeller, the degree of turbulence has a direct correlation with lower pump efficiency and greater hydraulic noise within the pump casing. To reduce the effects of turbulence before the water enters the centrifugal action of the pump impeller, suction pipes are typically kept as long and straight as possible before the connection onto the pump flange. Yet creating long lengths of pipe does not sit well with modern design trends which aim to keep mechanical rooms simple and compact.
Where a bend is connected directly onto the pump suction, the water flow may spin in opposite directions within the eye of the impeller. Pump energy then has to be spent correcting this action before producing the expected performance. Inevitably, both flow and pressure measurements will be less than those expected at the design stage. A simple alternative is to fit a type of strainer called a suction diffuser. A suction diffuser straightens out the spinning fluid created by the change in direction (bend) and enables pipework to be connected closer to the pump at a 90-degree angle. Eliminating long pipe runs, elbows and reducers makes for a smaller mechanical room footprint and optimum pump performance.
Designing mechanical rooms with grooved valves achieves the desired space savings. Having grooved check valves, close-directly coupled to grooved butterfly valves, eliminates the use of flanged spool pieces on the pump dressings and cuts out the need for flange adapters. Again, this reduces the mechanical room footprint. But space saving is not the only advantage: there are cost benefits too. When it comes to installation, avoiding an extra spool between valves means the job is completed more quickly so labour costs are reduced.
Cutting labour risk
Whilst material costs are relatively easy to fix, labour costs are more volatile, leaving contractors open to significant labour risk on project costings. The grooved mechanical system reduces that risk by a large factor and competes favourably on total installed costs because a larger proportion of the total costs is fixed. When other joining methods are used, typically 70% of costs are subject to variation making it difficult to estimate, which means a greater risk to the project budget. A grooved mechanical system with a quick and simple joining method and no need for jobsite preparation offers considerable cost-saving opportunities on installation.
Time spent on the jobsite is a critical cost factor, leading contractors to prefabricate as much as possible offsite. Prefabrication offers major productivity gains and labour efficiencies – especially when there is limited space on site. The grooved system lends itself to prefabrication, since pipes can be cut and grooved offsite and valves fitted to pump assemblies ready for final assembly in the field as needed. Working in such a way avoids the risk of loss or damage to components on the jobsite, whilst reduced material handling lowers the potential for accidents.
Time savings
Ease and speed of installation are key benefits of grooved mechanical room installations, since just two nuts and bolts are needed to form a secure joint. Once installed, the grooved system provides for quality control through visual confirmation of proper installation. Metal-to-metal bolt pad connection indicates that the joint is properly made and avoids time-consuming X-ray tests.
A system that uses grooved pipe-joining technology can be flushed out and cleaned in a fraction of the time needed for a system joined by other methods. When pieces of equipment need to be disconnected from the system – for instance to avoid flushing dirty water through a chiller – this can be done quickly and simply. A temporary by-pass around a chiller that might take several days on a welded system can be avoided with the grooved system and the task completed in a few hours. When it comes to cleaning filters and strainers after flushing, access is much quicker and easier through the loosening of two nuts and bolts and the way the filter is positioned in the strainer makes is easy to extract. Modifications to pipework which may be required at any stage during the project can be completed with similar ease.
Conclusion
Switching from welded and flanged specifications to the grooved method for mechanical room installations can make a big difference to the success of a project. And its use is becoming more widespread. Because manufacturers of pumps and some other types of equipment have come to realise the advantages of grooved technology, many now offer a grooved outlet as a standard option. Not only does it make for easier product testing in the factory, but manufacturers know that having a grooved connection reduces the likelihood of additional forces on the equipment that could damage it.
Engineers, contractors and owners all stand to gain from grooved systems. Design engineers can realise space savings; contractors can make time and cost savings to achieve on-time, on-budget hand-over to the client; owners get an efficient, reliable system which is easy to maintain.
Shaun Hughes is Regional Manager Southern at Victaulic