Press-fit proves its worth for gas supply lines
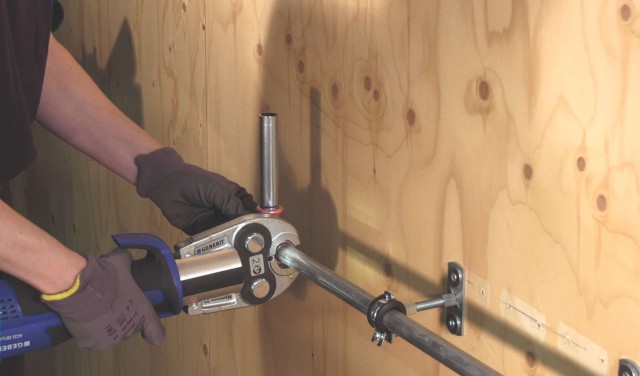
Offering quicker and safer installation, press-fit technology is proving to be a best practice solution for external gas supply pipework on high rise residential properties. Antony Corbett, Product Applications Engineer at Geberit, explores the benefits.
It is notoriously challenging for gas infrastructure companies to maintain, refit and refurbish gas supply pipework on high-rise residential properties.
Regular maintenance and periodic replacement is essential of course, whether for ongoing inspection or to replace leaks on screwed joints. However, with external pipework running up the outside of the building and feeding into individual properties, any work requires a series of safety measures. Contractors are often forced to close exits to ensure the safety of residents and restrict access to areas at ground level below the pipework. This is before you consider the challenges of working at height for the engineers themselves, often for extended periods due to the nature of the work.
‘IGEM/G/5 Edition 3 – Gas in multi-occupancy buildings’ sets the standard for gas installations both to and within multi-occupancy buildings, as well as the individual dwellings within such buildings. Pipes must be maintained in line with this standard, which covers a series of points including external and internal pipelines, the method of entry into the property, any movement (such as expansion, shrinkage or sway) of the structure in pipework design and the effect of altitude on pressure.
As a result, maintaining pipework for multi-occupancy buildings can take time. Traditionally, work is staged, largely to minimise disruption for residents, but there are more tall buildings than ever before in the UK (with even more in planning or construction) and maintenance programmes are in danger of becoming unfeasible as a result. The English Housing Survey shows that there were around 1.85million high rise flats in England in 2020 (8% of total housing stock).
With increasing demand and ever-challenging conditions, infrastructure companies are working closely with pipework manufacturers to seek alternative, innovative methods that can reduce the time spent on each property.
Press-fit – a more effective solution
One easy solution is to switch from welded, screwed or socketed joints to press-fit installations, which allows for quicker and easier installation and maintenance.
Press-fit is quicker to install than traditional jointing methods because it requires no hot works, no soldering and no threading. It is easier to fit (even at height) because engineers simply cut to length, deburr, mark up, mount the fitting and press. A pressing jaw with jaw guide helps prevent any risk of the joint slipping or being pressed in the wrong place and ensures reliable and durable connections.
A unique pressing indicator, which consists of a thin plastic foil encasing the pressing shoulder, gives a visible indication of a completed joint when the foil is removed during the pressing operation.
Press-fit system installations have long been estimated to take approximately 30% less time (if not greater) to install than their traditional counterpart methods.
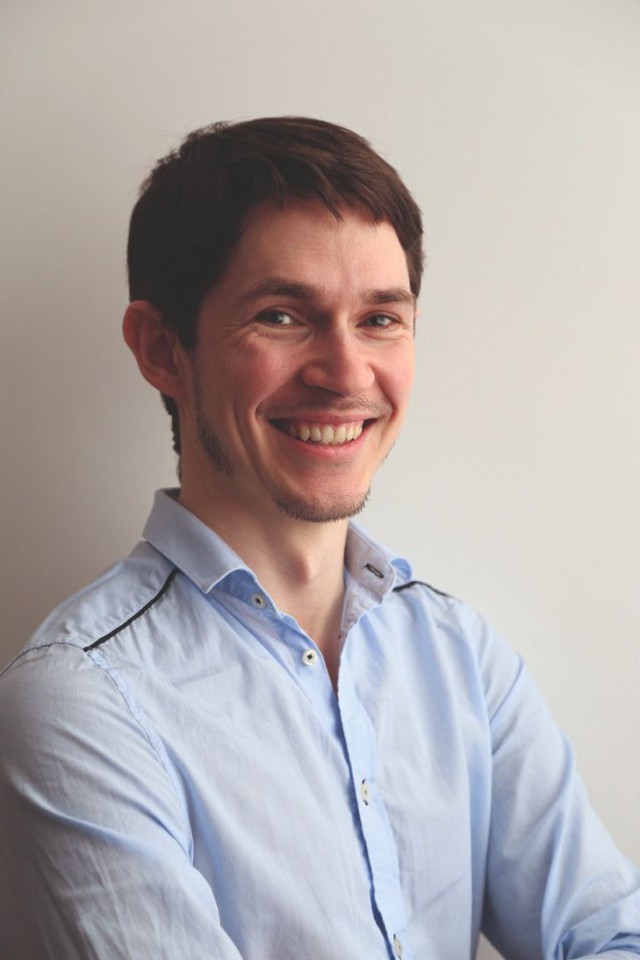
These are the kind of benefits that have led to press-fit systems being accepted as a viable method in the guidelines for one of the UK’s biggest gas infrastructure companies. The system is now in full acceptance throughout their network after six years of testing, piloting and discussions.
For example; with Geberit Mapress, engineers can check and repair the gas supply pipework for an entire high rise residential building in one to two days, which reduces time, labour costs and disruption for residents. Removing hot works from the job also improves safety both for contractors and for those on the ground.
Proven credentials of press-fit
Press-fitting is by no means a new technology and has in fact been available to installers for five decades or more. It is suitable for everything from domestic water and gas supply pipework, to solar installations, compressed air, fuel supplies and other industrial lines – with options across copper, stainless steel, carbon steel and CuNiFe.
As well as delivering a more cost-effective, time-efficient, safer job, it also improves reliability of joints too. Coloured pressing indicators are fitted over the ends of fittings, which offer easy identification of both the material and any unpressed joints during the installation process. The fitting and pipe are pressed only once the pipe has been inserted to the required insertion depth, which ensures a safe, dependable and long-lasting connection. There is no need for lubrication and the joints will leak until pressed to show incomplete pressing during pressure testing.
Another key application for press-fit systems in high rise residential buildings is for sprinkler systems, which continue to be a key topic of conversation following the safety changes to the building regulations.
For many years, retrospective installation of sprinklers into multi-occupancy buildings has been regarded as messy, disruptive, unattractive, and too expensive. With this perception from the construction industry - and without regulations driving the necessity of installations in existing buildings – it has been rare for systems to be added retrospectively to buildings.
In fact, with modern press-fit systems, the opposite is true. As we have learnt, press-fit systems offer fast, reliable connections, with no hot works – not to mention lightweight piping and a clean finish too.