Simultaneous operation – a chiller revolution
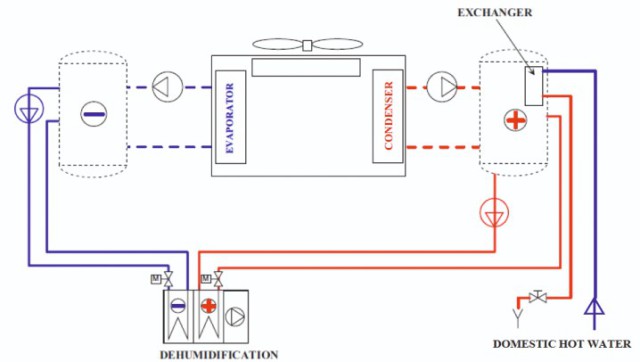
For the best part of 30 years, chillers were in danger of being left behind as the growth and popularity of VRF solutions began to dominate the market for comfort cooling in commercial settings. Darryl Smith, Managing Director of AUK Distribution, explains why chillers contain the technologies to now fight back.
Chillers have changed and the evolution in technology has given the sector a new lease of life, turning chilled water into a serious contender once more for many applications.
The benefits of heating, cooling, heat recovery, water production, and direct expansion (DX) connectivity have seen Variable Refrigerant Flow (VRF) used extensively for building services, reducing capital expenditure and achieving low operating cost of a building.
There are limitations, however. The capacities of modular VRF systems are generally limited to around 230kW and their footprint, when using multiple systems, can become quite large when available plant space is reducing. The amount of refrigerant circulating around a building can be high and the design hurdles to overcome potential refrigerant concentration legislation, if leakage occurs, can be expensive. This means that large building load demands often require something different.
The chiller market has developed highly efficient alternative solutions which lend themselves to the demands of modern building design. This has taken what was once a predominantly cooling-only product for larger capacity projects to a multi-functional mid-to-large capacity competitor.
Although the initial installation costs of a chilled water system may be higher than VRF, due to larger pipe diameters, pumps and flow regulators etc, the total cost of ownership over the lifetime of a system can still be competitive, and building design has little impact on the refrigeration circuit, meaning no issues with elevation or pipe length.
A chilled water or hydronic system works by pumping water cooled by the chiller through a network of pipes inside the building, and uses water in the terminal unit heat exchanger in place of the refrigerant found in a DX system.
While a DX system involves a heat exchange process of air to refrigerant and back to air, chillers introduce a further stage in the form of water. The advent of aluminium microchannel heat exchangers means the water can be cooled without having to use the refrigerant circuit in suitable ambient temperatures, offsetting any reduction of efficiency due to the additional heat transfer process.
The absence of refrigerant being moved around the building also means chiller-based systems bypass leak detection guidance (BSEN378), removing the need for leak detection systems in places of rest, such as hotels or student accommodation, which can add significantly to a project’s capital and maintenance costs.
With a range of 49kW to 1.1MW, 4 pipe air-cooled EnergyPower chillers from Clint offer dynamic design potential. The units are able to provide cooling, heating and domestic hot water at the same time and with the same unit. They are suited to buildings with the simultaneous need of ambient heating, cooling and domestic hot water, such as hotels and multifunctional buildings with service and residential users.
Models in the range covering capacities from 49-190kW and 167-634kW feature scroll compressors with axial fans (EC inverter fans as an option) and plate heat exchangers. As an alternative to R410A refrigerant, they can be supplied with either R452B or R454B. Units for capacities from 278-1133kW feature screw technology, shell and tube heat exchangers and axial fans, again with the option of EC inverter fans. As an alternative to R134a refrigerant, they can be supplied with R513A.
Simultaneous operation
We generally think of a chiller operating in a single mode as moving energy from one area and expelling in another; chilled water being a product of the evaporator in cooling and hot water via the condenser in heating. Generally, this energy would not be reusable and in turn lost to ambient air by the fan contained within the chiller chassis, acting to move air across the heat exchanger.
When operating simultaneously, hot water can be generated using the heat rejected from the condenser and chilled water can be provided from the energy absorbed by the evaporator at the same time. The fan moving air across the heat exchanger is stopped and energy is transferred between the two heat exchangers, maintaining the refrigeration cycle’s operating pressures. This method not only provides a purpose to serve mixed applications, but also improves the system efficiency; what would normally be ‘lost’ energy is reused.
Simultaneous operation can create a system efficiency of 8.8; that being 8.8kW of useful energy given out in terms of both heating and cooling in ratio to every 1kW of electrical energy consumed. These high efficiencies are not solely achieved from the concept of 4 pipe simultaneous systems, but also from the development of load control through both scroll and screw compressor innovation, inverter application and more complex control algorithms. We can make comparisons here with the simultaneous operation of a heat recovery VRF system, but unlike VRF there are no heat recovery boxes to install in the refrigerant pipework within the building.

By using a third heat exchanger, either within the chiller or within a thermal store, energy to produce domestic hot water can also be utilised. This adds an efficient bivalent source to a traditional boiler or removes the need for a boiler entirely. The applications lending themselves to simultaneous operation are residential and commercial comfort cooling and heating through 4 pipe fan coils or underfloor heating methods, domestic hot water use for hotels, leisure centres and spas, data centre cooling whilst providing heating and DHW to staff offices, or more industrial uses, in which chilled or hot water is required simultaneously in various forms through a process.
Chilled water systems can be used with a wide range of terminals and generally emit lower noise levels at fan coil units than can be experienced with refrigerant velocities in pipework.
Compressor technology
Turbocor compressors are a further example of how technology has improved both efficiency and reliability in chillers. A multiple-stage compression design has reduced what would typically be a large centrifugal compressor into a more compact variant, even compared to its positive displacement screw or reciprocating compressor alternatives.
With a low number of moving mechanical parts, the centrifugal compressor is an effective choice in any design. Because of its high rotational speeds - to generate an acceptable pressure difference - a large amount of friction is placed on the shaft bearings, which decreases efficiency and requires an essential source of lubrication. If the oil lubricating the shaft is not cooled sufficiently or develops flow problems, the result usually is catastrophic.
Danfoss developed the Turbocor centrifugal compressor with a fully integrated inverter control system and revolutionised efficiency and reliability with magnetic friction-free shaft bearings. This means that the compressor can operate without oil , removing the oil cooling circuit with no wear and tear on the shaft bearings. Sensor rings that can detect the shaft position 100,000 times per second also provide improved control and monitoring
Refrigerant choice
With a growing awareness of environmental issues, chillers also have the advantage of a range of refrigerant options. The refrigerant for DX is generally determined by whatever the system is designed with, usually R410a for larger applications due to the limited options available for R32 due to the flammability aspect and the concentration of potential leakage.
The opportunity to select from various refrigerants can allow the corporate responsibility needs of the customer to be met. With changes in using alternative low global warming potential refrigerants such as R452B, R454B and R513A, we now have products available to meet specification and regulation across an extensive array of capacities.
From being very much in the background not so long ago, this modern way of thinking for energy recovery and multiple-use products has given the chiller the push it needed to bring it back in line with the VRF possibilities, especially within the commercial market.
Darryl Smith is Managing Director of AUK Distribution