Making the net zero goal a reality
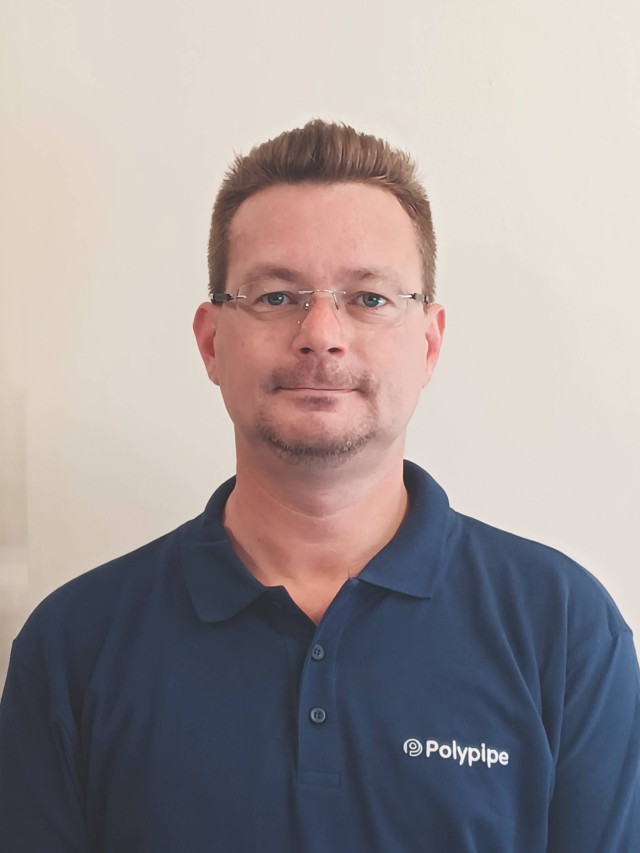
With the UK Government setting ambitious targets to achieve decarbonisation and net zero emissions by 2050, Alex Ashton, Environmental and Sustainability Manager from Polypipe Building Services, explains how manufacturers have a role to play in a low carbon.
The UK was the first major economy in the world to pass into law its objective of reaching net zero greenhouse gas (GHG) emissions by 2050, with the next major step to achieve a 68% reduction in emissions by 2030.
Clearly all industrial sectors across the UK will need to provide solutions to make this goal a reality, and as we all know the construction industry has a huge role to play. Indeed, the UK Green Building Council estimates that the built environment is currently responsible for 25% of total UK GHG emissions, rising to 42% if associated transport emissions are considered. Although this figure is falling, more must be done to ensure emissions reductions keep pace with our 2030 and 2050 goals.
An ambitious, structured approach is required from the entire supply chain to make this happen, not only in the more visible areas of GHG reduction such as energy usage but in all areas of operations. The likes of waste reduction, recycling and moving to a circular model for as many resources as possible will be key. Here at Polypipe Building Services we believe that manufacturers must play a vital role in taking action and helping the following supply chain to make the biggest possible reductions.
Addressing the different sources of GHG emissions
GHG emissions are typically categorised into three groups or scopes
Scope 1
Emissions are those generated directly by an organisation, for example; the burning of fossil fuels in a boiler or furnace.
Scope 2
Emissions are indirectly generated through the purchase of electricity, steam, heat, or cooling that’s generated elsewhere.
Scope 3
Accounts for the biggest portion of an organisation’s footprint. They are those generated from indirect sources but driven by the demands and activities of the reporting organisation. This is a very broad category that covers all emissions outside of Scope 1 and 2.
It’s important not only in how we measure our own footprint, but also how manufacturers like ourselves remain mindful of our impact further down the supply chain
In other words, whether it’s Scope 1, 2 or 3 for us, the benefit of reductions for our customers will be classed as Scope 3.
Genuit Group, our parent company, have committed to the Pledge to Net Zero and the Science Based Targets Initiative meaning that we will soon have science-based decarbonisation targets covering our scope 1, 2 and 3 GHG emissions. Progress towards our pledge to net zero is evidenced by our group-wide 46% reduction in scope 1 and 2 GHG emissions per tonne of production, when comparing fiscal year 2021 to 2020.
Minimising emissions

So how can emissions falling under Scopes 1 and 2 be minimised to the benefit of the broader supply chain? It’s important to see this as an ongoing, transitionary process rather than a single shift – examples include a move from diesel to biodiesel for our fleet of lorries, our sales teams’ next generation of company cars will be plug-in hybrid or all-electric vehicles, and we are trialling onsite electric counterbalance forklift trucks at our Aylesford facilities. These daily transportation activities all have a positive impact on emissions.
Where energy must be purchased, the first key step is to ensure power usage is minimised wherever possible. Beyond this, manufacturers should seek a zero-carbon supplier. As an example; Polypipe Building Services procure renewable energy via wind power through a Renewable Energy Guarantee of Origin (REGO).
Minimising Scope 3
Given Scope 3 emissions are the biggest source of emissions, seeking to reduce these must be a core focus. Central to this is considering the full lifecycle of the products we make down the supply chain.
- How can the sourcing of raw materials minimise emissions during their production?
- How can our own production processes and equipment ensure minimal emissions are created?
- How can these products be made so that they provide maximum durability during their useful life, reducing the need for replacements?
And… when they do need replacing? Final question, how can the materials be reused as part of a circular economy to avoid the impact of their disposal as waste?
The first step here is to ensure that as an industry we avoid unnecessary waste. So that only what is needed is produced with minimal left over from construction work requiring recycling. Offsite and modular construction have a key role to play here as they require much greater precision in what materials are needed, when and how. Manufacturers who offer a design service can ensure they produce precisely what the contractor needs, avoiding waste on-site while optimising how quickly the job can be completed. We anticipate this to be one of the fastest growing areas of our business in the next few years.
If a circular economy is achieved for the waste that remains, then the challenges of using less virgin material and that of avoiding waste to landfill are intrinsically linked. More reusable materials re-entering the production process means lower demand for virgin material that would typically generate higher emissions to extract and process.
Our aim is that a fully circular process could be established for many of our products, and that the same is done across the full spectrum of building products manufacturers. If this can be achieved, the knock-on effect for the GHG emissions of building services contractors will be dramatically reduced. It’s important that the waste hierarchy is applied across all operations. All offcuts from production should be reprocessed in house, whilst other waste materials including other plastic packaging and cardboard should be collected and sent to specialist recycling companies.
Furthermore, to maximise the amount of product that re-enters use we should look to build partnerships across the supply chain. We have recently begun a trial with some of our key merchant customers to make it as easy as possible for contractors to return PVC piping offcuts, obsolete products, plastic packaging, and bulk bags. These materials are picked up by our vehicles when empty on a return journey, further reducing emissions. This scheme has the potential to grow and provide an important route for waste to be recycled rather than disposed of.
Conclusion
Most companies appreciate the scale of achieving net zero, but capital support will be needed to make the changeover in equipment, machines, and vehicles to carbon-neutral electric for example. Pressure is building from policymakers to specifiers and consumers for our sector to decarbonise. It is essential that building services companies form the right alliances and partnerships now to both capitalise on the opportunities and mitigate the risks required to make net zero manufacturing possible.
Alex Ashton is Environmental and Sustainability Manager at Polypipe Building Services