Hunting for carbon
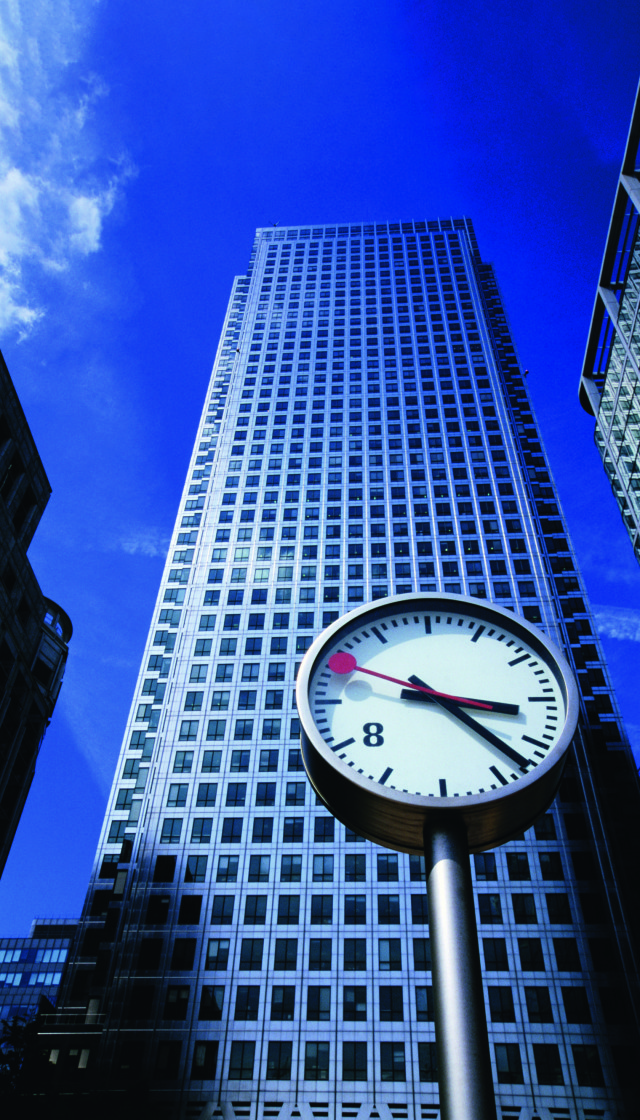
The pivotal role of the built environment in achieving global climate change goals was highlighted again at the recent COP27 gathering in Egypt, but David Frise, Group Chief Executive Officer at Building Engineering Services Association (BESA) points out that to reduce carbon emissions, you must first find where they are coming from.
The battle to ‘Keep 1.5 alive’ goes on. The 200 global leaders at COP27 made several commitments but ensuring the planet’s temperature does not rise by more than 1.5degC compared with pre-industrial levels remains on a knife edge.
To help meet global net zero targets, the United Nations has set two goals for the built environment, which is responsible for around 40% of total global carbon emissions, to achieve by 2030: First, that all[KC1] [ER2] new and refurbished buildings must be net zero in operation and second, that all new and refurbished buildings must achieve at least a 40% reduction in embodied carbon.
This attempts to address our most daunting challenge, which is tackling the performance of existing buildings. New buildings can be designed to meet the latest energy efficiency standards, but we replace only a tiny percentage of our building stock every year. A massive programme of refurbishments and retrofits across both the commercial and residential markets will be essential to get anywhere close to the level of carbon reductions needed to contribute to the 1.5 challenge.
Carbon targets should be a powerful motivator, but in truth, expressing this in terms of energy costs is more likely to bring about change. Persuading clients to invest in energy saving measures was a challenge when energy was relatively cheap, but the tripling and quadrupling of gas and electricity prices this year has dramatically changed the argument.
Complexity
Many businesses face collapse simply because they don’t know how to make their premises operate efficiently and cost-effectively. Often the complexity of how buildings consume energy and contribute to carbon emissions is hard to unpick – particularly as there are so many ‘sub-systems’ to consider that consume energy in the background, like supplemental heating, lighting, and air conditioning much of which might not have been part of an initial design.
Buildings have considerable ‘legacy’ systems that continue to play an important role but have not been checked and maintained so are operating well below optimal. Working out which systems are using most energy and locating ‘offending’ plant is a big step towards hitting those UN goals – and putting a huge dent in your running costs.
Systems need to be identified, refurbished, or replaced, and then properly maintained – this addresses both operational and embodied carbon. However, the built environment industry has always struggled to access the targeted data it needs to help building managers make informed decisions about upgrades, maintenance, and the ongoing efficient operation of their built assets.
The sector’s leading professional bodies have been wrestling with this problem for some time and are now collaborating to align the data standards that are used to manage costing, carbon and building and facilities maintenance.
Building Engineering Services Association (BESA), National Building Specification (NBS), and the Royal Institution of Chartered Surveyors (RICS) along with other interested parties, including government departments, have created a roundtable collaboration forum, to standardise the way data is gathered and shared that can improve life cycle costing, carbon assessment and digital led maintenance planning.
The Government Property Agency (GPA), which manages the government’s commercial estate, has been charged with delivering major efficiency improvements across its vast portfolio. The use of better building information is pivotal to this, and the GPA is working with the industry bodies to embed data standards into its estate, which can then act as a ‘living laboratory’ demonstrating the use of data alignment for specific information purposes, across the entire asset life cycle, to deliver ‘real life’ benefits.
The intention is that this will create a template for whole life costing and analysis for all built assets and deliver those much-needed energy and carbon savings goals.
“More than 80% of the total cost of ownership of any built asset is in ongoing operation and maintenance, but many clients find it almost impossible to get a clear handle on how much they should be spending and on what,” said BESA chief executive David Frise.
“Many building owners and occupiers tell us they are sick and tired of not having access to complete cost and asset specific data about how their buildings need to be designed and built in a way that will optimise how they are run and maintained. They now desperately need to cut running costs, whilst make sure their buildings are safe and compliant, and get on with delivering their net zero carbon reduction targets.”
Lifetime
The industry bodies are working together in a roundtable data collaboration forum to drive this forward. One crucial task is addressing the ongoing problem that cost cutting decisions made at the design stage often lead to higher lifetime maintenance costs, therefore passing on the problem to clients and people further down the supply chain. The dramatic rise in energy costs has put this weakness into sharp perspective.
The market for UK building maintenance is estimated at over £60 billion/per annum1, but the industry bodies fear that a significant proportion of that money is not being properly targeted to reduce running costs and carbon emissions, with inappropriate funds allocated to keep buildings operating safely and efficiently.
The organisations’ plan is to publish a cost and maintenance ‘playbook’ that will explain how quantity surveyors and FM/maintainers should set about gathering asset data using digital tools. To achieve this, they are bringing together SFG20, the industry standard for building maintenance developed by BESA, with the RICS New Rules of Measurement (NRM) for building works and the BIM Construction Classification (Uniclass) developed by NBS, along with CIBSE’s Guide M best practice guidance for management and maintenance of engineering services.
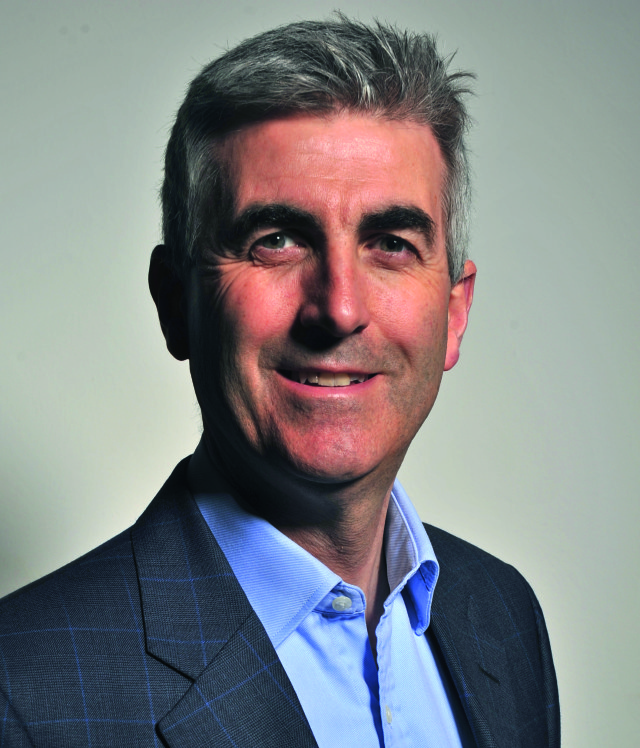
This is intended to bridge the gap between the collection of digital information at the construction stage or during refurbishment projects, to help building managers develop accurate asset registers that can inform maintenance plans, asset renewal/life cycle plans, and carbon assessments.
“BIM models contain 80% of the data needed to create robust maintenance programmes, but most surveyors are not using it – it is being lost at handover,” explained Frise.
By aligning SFG20 schedules with Uniclass classification and NRM 3 cost structures and CIBSE’s Guide M expected life tables, this can ensure the necessary information from ‘as built’ projects are handed over, to enable fully costed plans for the lifecycle operation and maintenance of buildings, saving precious time and money.
Uniclass is embedded in the BIM process, but all the industry data bodies have agreed that there is a major problem at project handover, which leads to much of that design information not being used in the surveys that establish maintenance schedules and upload data into CAFM systems.
Frise added that there was currently too much “guess work” involved in the production of life cycle cost plans, carbon assessment and maintenance programmes and, as a result, operation and maintenance is typically undervalued and, therefore, often “little more than a tick box exercise”.
As part of the process of aligning standards, BESA has developed SFG20 Resource Modeller, a tool that allows maintenance professionals to cost their requirements and identify exactly what resource is required, also helping to identify what is the defendable running cost needed for the set service levels and meet legal requirements and energy and carbon reduction targets.
The data alignment mapping work is well underway and, by bringing all the parties responsible for setting standards together, the group feels there is light at the end of the tunnel for achieving digitally enabled and fully planned and costed maintenance programmes.
“Getting this right will be vital for making our buildings more efficient, safer, healthier and to put us on the road to net zero,” said Frise.
*The leading professional bodies are:
BESA – the Building Engineering Services Association
NBS – the National Building Specification
RICS – the Royal Institution of Chartered Surveyors
Source
1 Economic significance of maintenance report 2022, BCIS.