The sophistication digital technology brings to project design

Gavin Statham and Mike Robinson of BES Ltd discuss Building information modelling (BIM) being used for all publicly funded projects, including healthcare facilities.
BIM is the construction approach comprising best practice processes to manage detailed information around the design and delivery of new developments. This is widely deployed in healthcare beyond the NHS, BIM is not just about delivering a smoother and more collaborative construction process through the control of information: it is also about ensuring the enduring value of an asset, which means developing a building that performs economically, with optimal smart functioning and minimal environmental impact.
The 2016 Government mandate on BIM requires a collaborative 3D approach, which has become a game changer for healthcare settings. Commissioning teams and facilities managers can now ‘explore’ a new facility, making it much easier to assess whether the design will work in terms of functional flow and personnel movements.
However, although 3D design is a significant part of the process, BIM can go well beyond 3D modelling. At BES Ltd we have developed an approach to working on projects with an integrated multi-disciplinary team, to provide a full ‘end-to-end’ turnkey service across design and construction. But now, we also utilise sophisticated digital technology that dovetails with our existing processes, allowing us to go much further in tailoring and maximising project delivery. We have made investments in software as these have been helpful in enhancing an efficient design, construction and commissioning process, ultimately delivering a faster outcome.
Working with clients including NHS Trusts and pharmaceutical manufacturing companies, such as AstraZeneca, we have found this form of digital twinning particularly useful in both healthcare and pharmaceutical projects, where they have contributed a real value by refining the BIM process to overcome some of the issues particular to legacy management and operational costs in this sector. By adding in extra digital technology, we can embed data that allows improved collaboration between both the estates team and the end users, including doctors, nurses, and patients, often preventing problems that may hold back the functioning of a facility.
Priorities in healthcare
Building validation and design for healthcare projects can be especially complex as particular consideration needs to be given to aspects such as patient safety and infection control. Facilities must be designed in line with ‘Health Technical Memorandums’ (HTMs) and ‘Health Building Notes’ (HBNs) specifications, while facilities for in-house pharmaceutical treatments must also comply with GMP (Good Manufacturing Practice) and MHRA (Medicines and Healthcare products Regulatory Agency) guidelines.
Key aspects that need to be taken into account from the start of the planning process in hospitals are patient pathways and clinicians’ requirements – clinicians will be concerned with robust details on how patients access and then exit the space in which their procedures take place. Spatial and equipment layouts are therefore critical, for example: the placement of the operating table in an operating theatre or laminar flow cabinets in aseptic pharmaceutical preparation areas; the flow of materials into a pharmacy and back out as a prescription; how people enter and exit an aseptic or cytotoxic preparation area within the constraints of the airflow pressure.
Lifecycle costs and a project’s carbon footprint are also crucial considerations.
While the involvement of clinicians in the initial design stage will ultimately deliver the best design for workflows, this hasn’t always been the case and has on occasion led to drawbacks in plans for some facilities. More significantly, though, traditional contracting models delivered by non-specialist companies without a full understanding of the HTMs have in some instances led to project failures, with particularly notable cases of this happening in the delivery of pharmacy aseptic suites.
This problem was highlighted in a 2018 NHS Improvement ‘Review of Pharmacy Aseptic Services’. The Review noted the increasing demand for on-site aseptically prepared treatments, at an annual growth rate of around 5%, and emphasised the ‘asset intensive’ nature of these services with the requirement for their ongoing maintenance and periodic renewal of the estate and equipment.
Tellingly, numerous common problems in the design of aseptic facilities that prevent them functioning as planned were revealed, including:
- low quality builds or delays in new facilities due to construction by contractors lacking ‘clean room’ experience
- insufficient local experience to plan, manage and troubleshoot projects
- lack of understanding of maintenance and service costs.
Digital tools
Digital tools are carefully chosen ‘bolt-ons’ that bring all the design information into one space. For example, the design is not just about the way the final facility looks: it has to take in practical aspects such as how much space will be needed for certain functions – or is available in a building that is being re-purposed, perhaps for plant such as ventilation and thermal control, all of which are particularly space-consuming in aseptic preparation areas.
The ‘BIM plus digital bolt-on conglomeration’ enables an effective interface between each process ensuring that all information is available in real time for both the delivery team and the client, as well as allowing calculation of running costs and energy efficiencies. All of the data that the manager needs to run the unit can be embedded into the model and the manual for the handover, aiding transparency and validation of all data. This ‘digital assembly’ also provides a regulatory function: for example, by supplying the extensive validation data for IQ (Installation Qualification), OQ (Operational Qualification) and PQ (Performance Qualification) required for MHRA approval for pharmacies and aseptic facilities.
3D visualisation
3D visualisation models are fundamental to working with clinicians and estates management personnel on the ergonomics they require, as well as benefitting subsequent facility management strategies. Revit can be used as a core 3D coordination, design and visualisation tool, which links to other programs.
The Revit model can be fed into Autodesk Navisworks Manage, converting it to a version easily read by all delivery partners, aiding clash prevention throughout the design and construction phases.
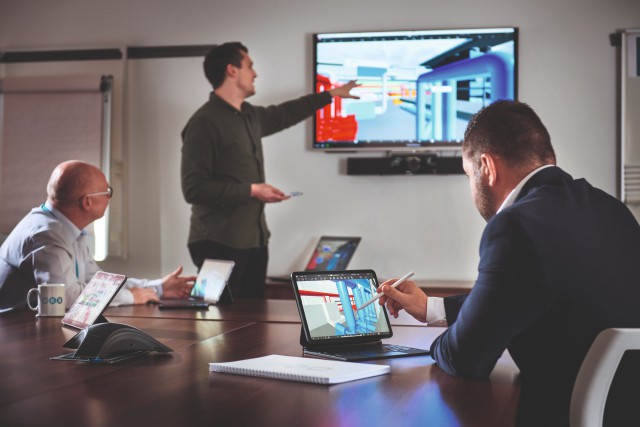
Avoiding downtime is always critical, Revitzo is a digital cloud-based collaboration/clash detection tool that pulls together BIM intelligence and allows all project team members to identify and manage any issues within the 3D model in real time. It’s highly beneficial to internal teams, enabling efficient collaboration on any type of project.
Another sophisticated visualisation system used is Lumion, which enables clients’ input into the design process. Using this tool, all stakeholders can experience the finished product, both visually and spatially, even in terms of particular finishes. This function allows user groups to respond to a design and their feedback to inform modifications.
Document management
Revit links directly to our internal document management system (DMS) Symetri’s Excitech DOCS, an open database that has been customised to interface with our existing processes.
Excitech DOCS, enables the management of all project documentation from schedules to invoices, and a CAD (computer aided design) interface that facilitates compliance, to industry standards according to the UK BIM Framework for the organisation and digitisation, of all information in the design and build process. As a DMS, its value is in the management of all project documentation.
The structure of documentation and workflows that are required by ISO 19650 are controlled within the Excitech DOCs environment, so the information generated can be easily pushed into a compatible CDE (Common Data Environment).
Facilitating mechanical design
Mechanical engineering requirements often form the backbone of a design. To speed up and increase accuracy and design verification, a digital toolbox should contain IES, a virtual environment analysis and performance modelling software. IES provides scope for mechanical engineers to optimise designs through much more complex calculations. This facilitates the effectiveness of a design through a pre-validation check, while computational fluid dynamics enable the simulation of airflows and eliminate dead spots. This improves energy efficiency to comply with the ISO 14644 standard and refine the design as often as required.
Compliance and customer engagement tools
To provide accurate specification information, NBS Chorus and Construction Information (CIS) software can be used.
NBS Chorus is a cloud-based tool that can be used on any device from any location to allow collaborative working across and with customer teams. Linked to Revit, this software enables design and specification in a single process based on manufacturers’ product data.
CIS enables verification of the design against all relevant standards, ensuring rectification of any non-compliance at the design stage.
Data fed into our Revit models also allows output into IFC (Industry Foundation Classes) and COBie (Construction Operations Building information exchange) formats, in turn feeding directly into Facilities Management Systems.
Gavin Statham is Business Development Director and Mike Robinson is BIM Manager at BES Ltd