Reviving aging infrastructure
Successfully optimising plant for a sustainable future - Dr Rob Lamb gives a case study in cold store refurbishment.
It’s estimated that the cold chain accounts for approximately 2–4% of UK GHG emissions. Data obtained from the UK Cold Chain Federation for 425 facilities registered with their Climate Change Agreement (CCA) Scheme during 2018 indicated that their energy consumption was around 3.5 TWh, with 96% of this being electricity. Considering there are almost 700 stores across the UK, the total energy consumed by this sector is likely to be closer to 5 TWh.
Over the last decade, the sector has made significant progress towards its commitment to the Climate Change Agreement, achieving a 16% improvement in energy efficiency since 2013 and exceeding the Government’s target of 12% compared to the 2008 baseline. However, more could be achieved as only 56% of facilities reached their energy improvement targets between 2017 and 2018.
During 2019/20 the sector made a considerable energy efficiency improvement of 19% against the Government’s target of 12% and the percentage of cold stores failing to meet the target was slightly improved from 56% in 2017/18. However, a considerable proportion of stores, totalling 52%, continue to fall short of achieving their energy objectives.
The Cold Chain Federation (CCF) are currently collecting performance data for the period 2021/22 for which the Government set an energy efficiency improvement target of 6.67%.
While the sector has shown significant progress in improving energy efficiency, recent benchmarking work conducted by Star Refrigeration indicated that even larger energy savings of between 30% and 85% are possible for new facilities (based on data collected from current Star customer installations). The research compared data for recent refrigeration installations with previous best practice figures published by the UK government and European wide research.
These savings can be achieved in new facilities through modern design, operational improvements, energy-reducing technology and the use of the latest construction materials. Existing facilities with old infrastructure may face further challenges, but improvements can still be made to contribute to the move to net zero.
Lead by example
Lineage Logistics’ visionary cold store refurbishing shapes a sustainable path. An example of this is their facility in Bellshill, Scotland. Built in 1971, it comprises three cold store chambers operating at -22⁰C, a +2⁰C chill chamber and an ambient loading bay. Cooling was provided by the original ammonia-pumped recirculation system, including four reciprocating compressors, one screw compressor (a recent replacement for a previous fifth reciprocating compressor), an intercooler, a low-temperature surge drum and two evaporative condensers, which were located on the plant room roof. Eight evaporators with manual hot gas defrost provided cooling in each of the freezer and chill rooms.
The plant was becoming increasingly difficult to maintain, particularly regarding sourcing spare parts, the greater frequency of breakdowns and refrigerant leakage. These issues affected the plant’s reliability and the risk of a large leak from the three-tonne ammonia charge system. Inherent inefficiency in plant components and the operation of one of the original freezer chambers at chill conditions contributed towards a high Specific Energy Consumption (SEC) of 30 to 35 kWh m-3 yr-1.
When looking at long-term solutions for the site, overhauling the existing system was considered but would require the majority of the plant to be changed. Plus, the site would retain its large ammonia charge. The option of integrating new equipment operating on low carbon synthetic refrigerants was explored, but the phase-down of the fluids under the F-gas regulation raised concerns about their future viability.
Back in 2019, they had installed modular ammonia packages at their Great Haddon facility, near Peterborough, which demonstrated improved efficiency compared to traditional ammonia-pumped recirculation plants. The Azanefreezer technology achieved Specific Energy Consumption (SEC) figures of 10 to 11 kWhr m-3 yr-1 and the final assessment was positive. It was accepted that the age and condition of the Bellshill facility meant that similar SEC performance was not realistic but previous retrofit projects provided evidence that savings could be achieved.
Modular, low-charge ammonia refrigeration programme
A programme to replace the existing central plant with modular, low charge ammonia systems was developed to substitute the existing central plant for the cold store and chill chambers. The cold store would be directly cooled using ammonia and the chill store would use a glycol secondary circuit.
Ultimately, each of the three cold store chambers was fitted with a modular, low-charge ammonia package and two evaporators. Additionally, cold Stores 1 and 2 were also equipped with booster fans to support air circulation due to the length of these chambers. The chill store included four coolers that were connected to a common glycol loop and two ammonia chillers.
Chill plant installation – circular economy
In an effort to reduce capital costs and improve sustainability through the use of circular economy principles, the chill plant installation used two ammonia chillers that were originally installed for a data centre application in 2007. Both chillers were refurbished and repurposed to provide cooling to the chill store. The refurbishment included overhauling the plate heat exchanger evaporators, screw compressor and replacing the obsolete PLC hardware.
A pump set shared by both chillers circulates glycol through the four air coolers inside the chill store. These coolers have a capacity of 66 kW each, based on a design air temperature of +1°C and glycol flow/return temperatures of -7.5°C/-2°C. Commissioning was completed in May 2021.
Freezer plant installation – heat recovery option
Retrofitting of the three cold store chambers was followed with installation of low-charge ammonia packaged systems, consisting of two economised screw compressors, a low-pressure receiver vessel, an air-cooled condenser, a four-way defrost valve, expansion valves and a stainless-steel electrical panel with a PLC controller. Liquid and wet return carbon steel pipework runs from each package to two aluminium tubes and fin air coolers which are mounted on the underside of the ceiling in each cold store.
Two of the three packages had been installed at a project in the south of England the year before but never put into operation. They were purchased and moved to the site to provide cooling to Chamber 1 and 2.
The plant serving Cold Store 3 was equipped with a fully welded plate and shell heat exchanger partial condenser. The condenser offers free heat recovery to generate warm glycol which is circulated through a break-loop and delivered to the underfloor heater mat glycol flow and return headers serving all four chambers.
As part of the project works, the client installed new insulated roofing panels on top of the existing cold store ceilings to provide better thermal performance and a reduction in air infiltration. Other energy-saving measures were also adopted by the site include LED lighting, door alarms and strip curtains. This further demonstrated the site’s commitment to reducing energy consumption and carbon emissions.
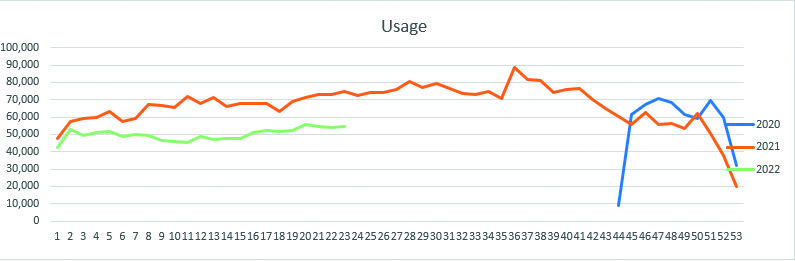
The plants were commissioned over three months from June to August 2021, starting with Cold Store 1, then 2 and finally Cold Store 3.
Performance Analysis
A comparison of energy performance before and after the installation works was carried out using the site’s energy meters, which showed a year-on-year reduction in power consumption. Weekly savings varied between 9% and 36%, with an average saving of 20%.
• The use of aluminium evaporator tubing and the low overfeed, low-pressure receiver system design which results in a 6 K approach between air on and ammonia evaporating temperature without the need for liquid pumps.
• All evaporator and condenser fans are EC type, varying speed and energy based on the cube law in proportion to cooling and heat rejection demand.
• Floating head pressure control which varies both fan speed and condensing temperature based on demand and ambient temperature.
• Fixed speed, economised screw compressors operating at 100% capacity at all times to maximise efficiency and avoid the 3% losses associated with inverter drives.
• An integrated PLC software that monitors the main energy-consuming components in the system and optimises performance by controlling the starting, stopping and speed of components based on ambient temperature and cooling demand.
Since the installation of the new equipment, temperature compliance has been maintained across all four chambers and issues relating to plant reliability and refrigerant leakage have been eliminated. Annual maintenance spend has also been reduced by 60% due to improved reliability, the removal of spend on spares and the ability to monitor plant performance off-site. Water and associated water treatment chemicals have also been avoided by switching to air cooled condensers and health and safety has benefited from a reduction in ammonia charge from 3,000 kg to 612 kg spread across the five systems (180 kg per Azanefreezer and 36 kg per ammonia chiller).
Monitoring of ongoing plant performance
From both a commercial and environmental perspective, it is essential that performance is maintained into the future. To guarantee optimum operation over time, the performance management software, Ethos, was installed. The AI software exports data from a plant’s control system to a cloud-based model. Here the data is analysed to identify deviations from optimal design conditions. This ‘digital twin’ approach enables a comparison of actual performance versus theoretical performance based on ambient and load conditions. Any differences in operation are reported and translated into remedial actions and projections of future energy consumption if no action is undertaken. This enables operators to understand the energy and financial implications of any changes made alongside energy and carbon savings estimates. Remedial work can then be monitored and improvements can be demonstrated.
Specific Energy Consumption (SEC) Forecasting
Since the completion of the Bellshill installation, the new ammonia chill and cold store packaged system PLC software has been enhanced to provide real-time predictions of SEC. This takes ‘kWhr yesterday’ data from the plant and produces an annual SEC figure where 365 days of previous data is available. Short, medium, and long-range predictions are also generated based on smaller data sets of 10 days, 90 days and 270 days, respectively. Tolerance varies from +/-30% when using 10 days of data to +/-5% for 270 days.
The short and medium data sets provide a swift indication of recent changes in energy performance caused by changes in plant operation (e.g., setpoint changes), a deterioration in component performance (e.g., compressor wear) or changes to site operating practices (e.g., poor door management). This means that preventative measures can be quickly enacted to benefit the annual energy performance.
This software had been installed at another site within the estate and an example of the output can be seen in Figure 10. The long-range forecast shows the quick change in SEC prediction when changes were made in February and then in March.
The predicted SEC for Bellshill based on data collected from site is between 20 and 22 kWh m-3 yr-1, which represents an annual saving of 30% when compared to the previous central plant. Further improvement could also be possible through repair and replacement of the building fabric to reduce heat gains.
Conclusions
Retrofitting modern, low charge ammonia cooling technology to a 50-year-old facility has delivered both environmental and financial benefits while providing long term peace of mind with regard to operational reliability and operating costs. Reusing factory-refurbished refrigeration equipment has avoided the need for around 80 Tonnes of fresh raw material and prevented components from entering recycling and waste streams before end-of-life. This demonstrates good circular economy practice, highlighting its effectiveness for business, people, and the environment. The project has successfully demonstrated that energy improvements can be made in existing facilities through the implementation of modern, modular, low-charge ammonia packaged systems. An energy assessment has indicated savings of approximately 20% in the first part of 2022 and an algorithm has predicted this could be as high as 30%. Operating savings have been realised through reduced maintenance costs, elimination of water usage and treatment chemicals for evaporative condensers.
The site’s total ammonia charge has been reduced from 3,000kg to 612kg, split across five modular systems, ensuring customer safety and that of the surrounding businesses.
The collection of data and the use of an algorithm to predict annual energy performance are providing early signs of performance drift, enabling swift action to be taken. This software can be applied to any control system where energy meters are fitted and be used to drive efficiency improvements. By doing so, companies will maintain their performance long into the future and contribute towards the UK’s net zero targets.
Dr Rob Lamb is Group Sales and Marketing Director at Star Refrigeration