Time to rethink pump upgrades

Matthew Blackmore, Head of Business Development at Armstrong Fluid Technology, discusses potential benefits in applying new approaches to pump replacement.
Replacement of pumps is a key part of any energy upgrade but, in so many cases, opportunities for significant carbon and cost reductions are missed due to outdated thinking. Connectivity and other aspects of technology have moved forward rapidly in the last few years, and applying new approaches to pump replacement can transform the business case for investment and significantly improve the lifetime performance of the upgraded system.
Applying traditional approaches to pump replacement can involve a number of pitfalls including:
- Failure to obtain sufficient information prior to specifying and installing the pump
- Installing unnecessary duty/standby
- Unnecessary pipework, components and inertia bases
- Obtaining better information during the design phase
Digital twinning can now bring the power of artificial intelligence (AI) to HVAC design. This creates virtual representations which can function as the real-time digital counterpart of a process. In addition to the usual data such as room dimensions and building load, digital twinning anticipates temperature, pressure and flow throughout the hours of the day, right through to the specific weather-related data for the specific location across the entire year.
Extremely detailed calculations of system operation, energy consumption and carbon savings can therefore be created. The technology is also powerful enough to allow alternative scenarios to be compared, by replacing key system components. For example, a system designer can rapidly receive a quantified report on the impact of introducing heat pumps, or replacing a specific pump model, with actual calculations
of the resulting savings in energy consumption, energy costs and carbon reductions provided by the technology in minutes.
Using these insights the simulation also calculates the payback period and return on investment. After installation of new or upgraded systems, the performance and resulting savings can be verified/proven using the same digital twinning technology. Leveraging cloud computing makes it possible to carry out calculations that were never possible using traditional computer simulations.
At last, important technical and financial decisions can be analysed comprehensively in advance, and based on a firm scientific basis.
Understanding operating conditions of the system (and saving energy) whilst planning the upgrade
We all know that energy upgrade projects can be a slow process. It can take as long as a year and a half for a capital expenditure energy upgrade project to reach the implementation stage, and whilst these discussions are taking place, not a single kW of energy is being saved. In addition, estates managers are having to battle on with inefficient, ageing and/or unreliable HVAC plant.
A far more effective way of approaching energy upgrades is to harness embedded intelligence of today’s HVAC pumps to track and collect data with greater accuracy than traditional flow meters. By approaching the energy upgrade in phases, and installing the new pumps ahead of the rest of the project, the pumps themselves can supply the necessary data, with a high degree of detail and accuracy. Most importantly, building owners and occupiers can start to save energy from day one, month one of the initial discussions. The building and load-specific information obtained via the pump software identifies opportunities for system optimisation with high cost/benefit ratios. This assists product selection and system design for the upgrade project, whilst actual, measurable energy savings are demonstrated in real time, throughout this process, to provide a more persuasive business case for stakeholders. Depending on the system and load profiles, total energy savings of up to 40% are possible via this approach.
Avoiding unnecessary standby
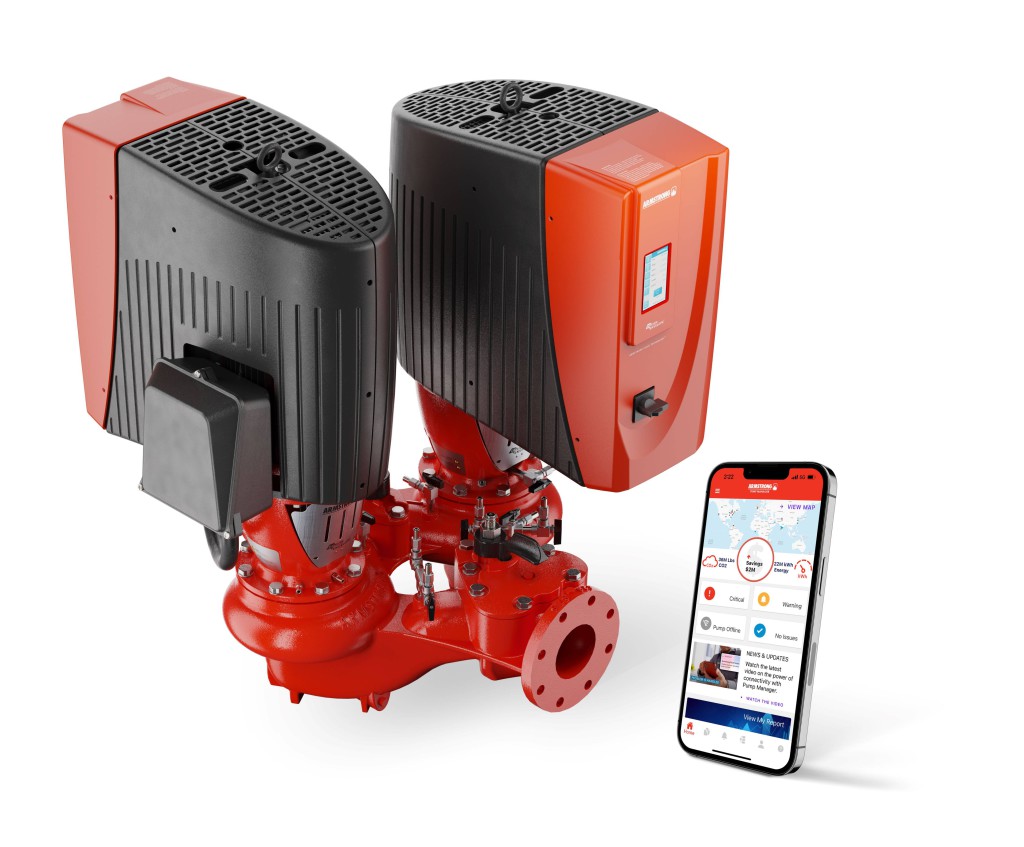
The practice of specifying full duty/standby pump installations is so widespread that it has not traditionally been questioned.
On a day-to-day basis, one pump (sized for full duty) is operational while another of the same size is out of action, simply there to accommodate 100% redundancy in the event of routine maintenance or pump failure. This has a huge impact on embodied carbon and cost.
In medium reliability installations (such as hotels, offices and retail stores) or sites considered as having a low risk (such as schools and apartment blocks) there are far more sustainable, efficient and cost effective ways of safeguarding pump operation than having pumps standing idle ‘just in case’.
Adopting a parallel pumping strategy (specifying two smaller pumps, each sized for 50% of the design flow) in preference to a 100% standby approach, can reduce first installed and lifecycle costs, free up space in the plant room or energy centre, and potentially halve the embodied carbon for the installation. The Armstrong Tango range of pump solutions, for example, incorporates built-in parallel sensorless pump control and embedded intelligence and connectivity for parallel pumping. These models can deliver energy savings of more than 30% and can significantly improve lifecycle costs.
And when you’re considering embodied carbon, don’t forget that the bodies of some legacy pumps can be left in place, with just the controls themselves being upgraded. This can save downtime and cost, minimise disruption and have a major positive impact on embodied carbon performance.
Avoiding unnecessary pipework, components and inertia bases
It is also easy to overlook aspects of cost, physical footprint and installation time when planning an energy upgrade. Firstly, look for pump components which perform multiple tasks with a single component. Armstrong Suction Guides and Flotrex valves, for example, perform multiple flow conditions tasks, at the pump inlet and discharge outlets, with single components.
Secondly, check that the upgrade is not going to involve unnecessary time and cost for the creation of inertia bases. Pumps such as the Armstrong 4300 models, for example, are designed to be pipe-line hung as an integral component of the pipework. This eliminates the cost of inertia bases, springs, flexible pipe connectors, field grouting and alignment.
In conclusion, an energy upgrade is an extremely valuable opportunity to futureproof a building. Don’t overlook these valuable opportunities.