Chewing the FAT

Keith Barker, President of the Commissioning Specialists Association, argues in favour of the factory acceptance test (FAT), but believes it needs to evolve to bring better value to modern projects.
In the world of building services equipment, the factory acceptance test (FAT) for major items of equipment has long been a staple of the pre-installation phase of a project. Many an hour has been spent by numerous people standing in a drafty factory while the equipment manufacturer strives to prove that its latest, new-fangled bit of kit can meet the consultant engineer’s specification – a specification that all too often has been cut and pasted from a mishmash of the last 20 projects and bears little or no relationship to the employer’s requirements.
Let’s be honest. Such tests may well have been insisted on merely to justify another jolly at someone else’s expense. Many readers of this article will be able to regale their colleagues with tales of daring do and epic bar sessions in back-of-beyond hotels. And that’s not to mention the almost inevitable travel ‘adventures’ that such escapades involve.
So, yes! Those sorts of FAT would seem to have little or no place in today’s smart, energy and cost-conscious construction industry.
But wait. That can’t be the whole story, surely? Well, no, it isn’t. Yes, it is important to understand the basis on which the equipment has been selected. Yes, there is a need to prove basic plant performance. But, more importantly, there is a need to make sure that the equipment will fit into the system. “System? What system?”, you ask.
Mechanical, electrical, instrumentation, controls and automation (MEICA) elements in today’s buildings cannot be looked at purely as discrete installations that work on a standalone basis. Making buildings work (no apologies for getting the CSA motto into this article) depends to a very large degree on getting those various MEICA elements to properly interface with one another in one complex system. And that’s the rub.
By the time anyone thinks about that aspect the design is often pretty much fixed. Frequently, the major plant items have already been decided on, may well have actually been procured and are in construction. Sadly, there is a good chance that there has been little thought as to how those plant items will operate in the completed building. And we are not talking about such things as the chillers in the cooling system or the boilers/ CHP units in the heating. We’re talking about the wider scope of MEICA items communicating with each other across system boundaries.
Communications backbone
Pretty much every building of any significant size has a communications backbone running through the building that is used to carry plant and equipment data as well as things like IT and telephony traffic. So, the first question is whether or not the equipment communications protocols are compatible with the planned network. Hands up if you’ve just thought “It’s all done with Modbus”.
Yes, but which type, RTU, ASCII or TCP/IP? And which interface is being used, ethernet or serial. Did I say serial? Which one did I mean, RS232, RS422 or RS485? What is the data baud rate? If it’s being transmitted at 115200 baud but the receiver is only capable of 9600, there is a good chance there will be issues. As if it’s not hard enough to get things to talk to each other, there is also the issue of finding the right bit of information or setting causing an issue. A recent problem revolved around a fairly basic chiller not talking to the BMS correctly. When the chiller manufacturer came to site to assist with the solution it was casually mentioned that the chiller’s internal controls had in the region of 700 parameters and any one of them could be incorrectly set.
These sorts of problem are sadly not uncommon on projects. CCTV cameras in lifts that are incompatible with the other cameras in the building; power consumption meters that can’t talk to the BMS; light fittings that don’t communicate with the lighting control software; a fire detection system that won’t trigger the PAVA alarm function or accept inputs from the fire suppression systems. Odds are that all of you can quote similar experiences.
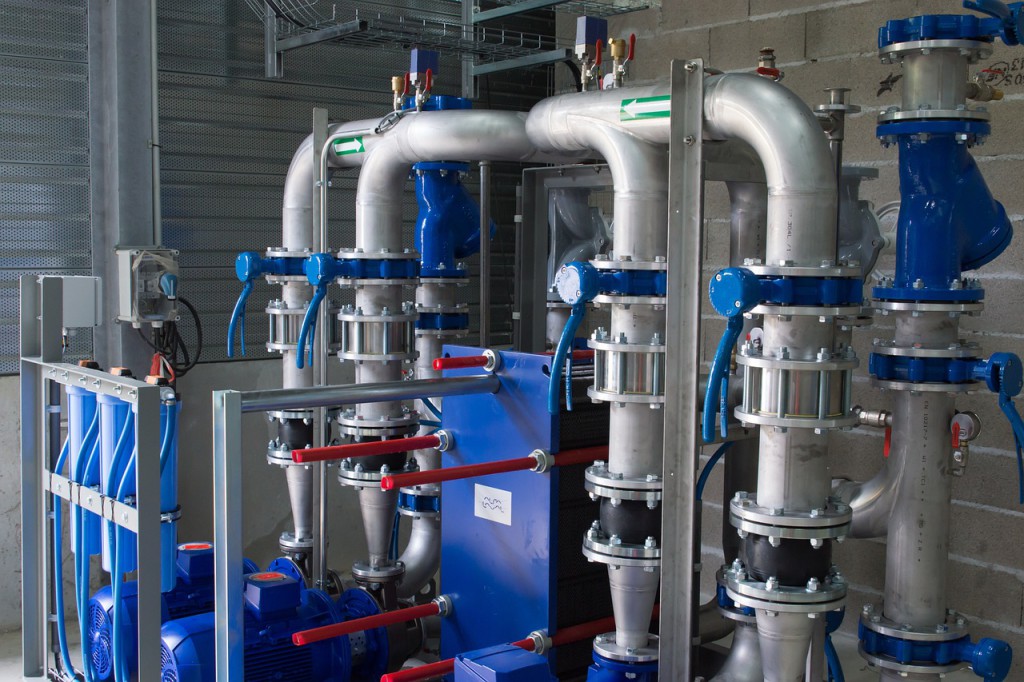
Interfaces and dependencies
So, what’s to be done about the situation? If you think about it, it is purely a matter of coordination. The thing is, who is best placed to manage that coordination? The client has the big picture of what they want in the building. They’re missing the necessary detail. The design team understand the principles of the individual MEICA components, however, may not be fully aware of all the ramifications of the necessary interfaces and dependencies. The main contractor is likely to be fully involved in making sure the subcontractors are being brought on board in a timely fashion and that the initial works are following the plan. The CSA suggests that the commissioning management team are the obvious solution.
CIBSE Code M calls for the commissioning management function to be in place very early in the construction process. It is still far too often the case that the commissioning management team is not in place until RIBA stage 5 – stage 4 at best. If they are brought in much earlier, they can use their expertise to map out those critical interfaces and dependencies. They can then ensure that elements are built into the factory tests to prove the compatibility of equipment.
Of course, it’s not quite that simple. For example, to test whether the LV panel circuit breakers or consumption meters talk to the BMS you’ll need a BMS node connected to the LV panel and a BMS person with a laptop (or a data link to that person in their remote location....). But the additional organisation isn’t that hard.
Additional cost
Let’s be honest, there is likely to be some additional cost. Now, this is important. It’s about time the construction industry, as a whole, accepted what common sense has been telling them for the last four decades or more. Spending a little more money up front to make sure things work properly when brought to site will save lots of money and time solving problems further down the line.
The upshot of the above discussion is that no, the FAT shouldn’t be killed off. The ‘but’, of course, is that it needs to evolve to become more relevant to today’s MEICA environment and to be of better value to the project – and thus the client who is paying the bills.
Just one final point. Attending a FAT via video link? If it was being run by a professional TV crew with all the relevant hardware and facilities then maybe, just maybe it’s feasible. But eight hours on a Teams call (other video conferencing software is available) trying to see/hear what is going on? Not a good idea!
So, keep the FAT, but use the expertise of your commissioning management team to include communication and coordination testing. It will be a good investment!