Getting connected with modular wiring

Despite their initial high capital cost, the speed and ease with which modular wiring systems can be installed makes them a major cost saver — and their popularity continues to grow. Clive Humphrey of Wago takes up the story.
Modular wiring has existed in the UK since the mid-1990s, but it was not until the early 2000s as more manufacturers began to offer modular solutions that the concept became widely known and accepted.
On the face of it, modular wiring — sometimes known as ‘plug and play’ — is a simple idea. It replaces the traditional method of electrical installation using cable preparation on site with pre-made lengths of lead with mating connectors already fitted. Some people may still have doubts, but the dozens of successful and high-profile projects that have been completed show that modular wiring is no short-lived fashion.
Manufacturers of modular wiring fall into two categories — those that manufacture their own connectors and those that don’t. Those that don’t will use connectors made by those that do, so quality of connection is never an issue. However, it is important to be aware that not all manufacturers’ connectors will mate together.
Some suppliers just offer leads and connectors for lighting and power, whereas others provide a solution from the distribution board with home runs, main distribution boards and lighting distribution modules. Armoured leads offer mechanical protection in the form of flexible conduit for power connections with non-armoured ‘soft skin’ leads for lighting. In short, some manufacturers are component suppliers, others project suppliers.
Whoever provides the system, the benefits are the same.
The biggest benefit is saving time and money on site. This is not just something that manufacturers’ marketing departments promote but a true benefit of modular wiring. The material cost will be higher, but the saving in man hours on site far outweighs that cost. By its very definition, a modular system plugs together, which makes installation much faster and safer. And reduced installation time means reduced site costs. Overall it is possible to achieve a 40% cost saving using a modular wiring system.
Planning and design is done in advance rather than on site. The design starts at the same place, with the specification and CAD drawings from the client; the drawings are then ‘modularised’ and the take-off (bill of materials) produced. It is important, of course, that the supplier understands the specification of the project.
Material costs are controlled, and there is no wastage on site. Upfront costings ensure that the client or installer knows the cost of the modular wiring system and only the parts required will be delivered to the work area.
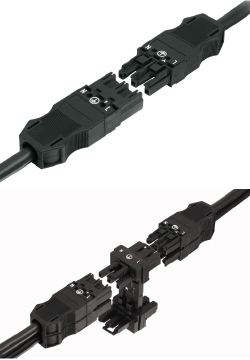
Every modular wiring system is prefabricated and tested offsite in a clean factory environment where wire preparation is accurate and connections reliable. Very importantly, every item from lead to home run is tested before it leaves the factory. Thus, the quality of what arrives on site is assured, and every reputable manufacturer will have a quality system to prove this.
In addition, delivery will keep pace with the progress of the building and can be adjusted to suit any changes. Parts are packed and labelled per floor or room, reducing the need for on-site storage. Packaging can be reused to reduce waste, and the absence of cutting and stripping can improve site health and safety.
The benefits don’t just stop at installation. As well as taking out initial cost, a modular system introduces flexibility during the life of the building. Modular connection makes extending or modifying the existing arrangement easy to achieve, whilst maintaining the same high standard. During a refit, for example, changes take less time, so business can resume sooner. As more clients see the benefits of building control and monitoring, such systems can be integrated into the pre-installed modular wiring system with the minimum of disruption.
There are clients and installers which still express some reservations about modular wiring. These should not be ignored by manufacturers but should instead be embraced in order for the industry to move forward. There can be concerns about availability of parts when faced with a project deadline. Such concerns can be overcome through experience and forward planning.
It is true that modular wiring lends itself to a repetitive design found primarily in classroom or hospital ward layout, but to overlook it for other projects is to ignore all the other benefits that it brings. On-site installation does not always follow the CAD drawings which, on the face of it, defeats the object of forward planning. However, well trained installers who have a close relationship with the modular-wiring supplier can ensure that this is avoided and effects or delays are minimised.
The advantages of prefabricated modular wiring are well proven, and these systems have been shown to provide outstanding flexibility as well as major cost-reducing and time-saving benefits. As we move towards greater integration, control and intelligence within buildings, whatever their size and type, modular wiring systems are showing themselves to be invaluable.
Clive Humphrey is product manager for interconnection products with Wago.