CHP — cost effective and energy saving
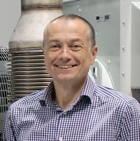
Combined heat and power (CHP) can often provide a very cost-effective energy-saving solution for hotels and leisure projects, says Chris Marsland of Ener-G.
In hotels and leisure applications, where there is a consistent heating or cooling demand over extended hours, the cost and carbon saving benefits of cogeneration are often unequalled. The technology is also very versatile, as it is just as applicable to new-build developments as to existing buildings, where it can replace ageing boilers or augment existing or new boiler plant.
The current tax saving benefits of CHP add to its attraction, including reduction or exemption from the Climate Change Levy and qualification for Enhanced Capital Allowances.
CHP can also help improve BREEAM ratings to increase planning compliance.
CHP can deliver an impressively fast return on investment within three to five years, but it won't deliver for every project, and detailed feasibility assessment is required to ensure the economic viability of CHP and obtain financial approval from investors.
There are seven steps to completing a detailed economic feasibility study.
1. Establish energy consumption data
The first step is to establish how the site currently consumes its electrical and thermal energy. This information is vital to accurately sizing the CHP system to meet the existing loads and, therefore, maximise energy savings.
Size matters. An undersized CHP system will operate at full load, but will not achieve the potential energy savings and reductions in carbon emissions. Oversized systems operate uneconomically and inefficiently at part-load, which reduces efficiency.
Data can be extracted from a combination of building energy management system, current and previous years’ energy bills, half-hourly meter readings from the supplier and short-term monitoring/metering.
2. Calculate energy load profiles
This energy data can be used to calculate the site’s load profiles, which reveal how and when the site uses its energy — the times of the day, week, month and year for the highest and lowest demands. Plotting the number of hours at which specific loads are experienced also produces load duration curves. These are useful for examining if the recommended minimum 4500 h per year heat load is available.
3. Check the indicators
Load profiles are used to calculate the site’s heat-to-power ratios. A ratio of 1.5:1 is a good indication that there is a suitable level of on-site energy demand for CHP.
Another major financial viability indicator is spark spread, which is the difference between the incumbent electricity tariff and the cost of the input fuel. A spark spread of between four and eight is positive.
4. Initial suitability checks
Factor in the following.
• The site’s current electricity and gas tariffs — prices needed for cost calculations.
• Is existing equipment such as on-site boilers operating efficiently?
• Are there any energy-efficiency/demand-side measures being considered on site that could affect future energy loads?
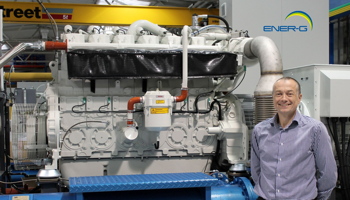
• Is the site planning a major expansion in the near future?
5. CHP sizing
CHP systems are often sized to meet the site’s minimum demand or baseload, to ensure maximum operating hours. As such, the CHP operates as ‘lead boiler’, with secondary boilers also supplying energy at peak times.
It may also be worthwhile considering a larger CHP to operate at maximum electrical or heat load output, exporting surplus energy when required, but preferably utilising or thermally storing extra heat.
Another option is to size CHP systems to load follow or ‘track’ the site’s actual electrical or heat demand.
CHP systems for new schemes, such as building developments or district-heating networks where energy consumption data isn’t yet available will need to be sized using comparison data from similar existing schemes or by using modelling software.
There are cost consequences for each sizing option, which need to be carefully examined using the accurate load profile data.
6. Practical and environmental considerations
The project’s estimated capital-cost expenditure and operating costs will need to include such factors as the cost of the installation works and the annual maintenance costs. Check the following.
• There is space on site for installation, and for maintenance access.
• Fuel supply is available and at the correct capacity.
• The local electricity grid can support generation.
• Electrical and heating connections are in close proximity.
Also consider the environmental aspects of the CHP system installation, such as planning conditions and noise restrictions.
7. Financial report
The final hurdle is producing financial calculations to convince the customer/investor of the economic and environmental benefits of the proposed CHP system. This report should indicate the estimated costs and the expected return on investment in terms of the anticipated payback period, or internal rate of return and the net present value discounted cash flow analysis.
Chris Marsland is head of cogen product and technology for Ener-G.