The pressing need for training
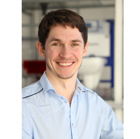
Press fitting is fast becoming the installation method of choice for installers keen to achieve a professional, speedy and reliable turnaround on both large and small jobs. But despite its simplicity, training is still essential in order to let installers get the best from every application.
![]() |
Getting to grips with press fitting technology |
Traditional jointing methods can be cumbersome and difficult to implement, and in many cases simply unsuitable and impractical for the job at hand.
The requirement for hot works is often an inconvenience at best, and an impossibility in some cases due to the site conditions or safety regulations, not to mention the cool down period which can add unnecessary time to any soldering job.
Press fitting offers numerous benefits for the busy installer. Coloured pressing indicators offer easy identification of both material and unpressed joints, with reduced flushing time and a cleaner installation process. There is also no need for lubrication and joints will leak until pressed to show incomplete pressing during pressure testing. This means there’s no need to drain the system as it can be fixed wet.
Press fit systems have been proven to take 30% less time to install than their traditional counterparts according to a BRSIA report, helping reduce the cost of jobs by approximately 27% compared with screwed steel pipework.
![]() |
Getting to grips with press fitting technology |
Despite its simplicity, pressing is by no means a job for the unskilled tradesman. As with any installation method, comprehensive training is vital to ensure that installers get the most from every application and to protect the standard of installations. Which is why leading manufacturers continue to invest in their training programmes for the benefit of those in the trade.
Much more than a product sell, these training programmes should combine best practice methods with specific product knowledge required to maximise the quality, speed and integrity of every single installation.
A good training course will also cover both the supply side and drainage side, giving installers the opportunity to see the benefit of press fitting over soldering. Often this provides the insight they need to change their method of installation.
The big questions Geberit answers three of the most commonly asked questions about press fit pipe systems. 1. Isn’t press fitting more expensive? How are we expected to pass that cost onto our customers? It’s important to consider the project cost – and to get your customers to think the same. With press fit there are fewer additional materials, you can get the job done quicker so it saves on labour and it’s also a cleaner, tidier, less disruptive job. In virtually all cases the overall job cost benefits will outweigh the material and even tool costs. 2. If the pressing tool needs calibrating, won’t I be left unable to work? The pressing tool needs calibrating after an initial two years, then every year after that. We like to think it’s similar to a service on your car – essential to maintain performance and quality. Geberit works proactively to mitigate the impact for installers, with links to hire companies for example that can provide short-term solutions. It’s all about forward planning – think ahead and you’ll keep disruption to a minimum. 3. Soldering is a craft – isn’t press fitting just de-skilling the industry? Quite the opposite. Despite its simplicity, press fitting remains a highly skilled process and that’s why we continue to invest in our training programmes. When people start to think that anyone can do it, that’s when corners are cut, and mistakes are made. This innovation isn’t about de-skilling, it’s about saving plumbing and heating installers time – which means more profit. |
Installers should ask the manufacturer about the tools required to use a press fit system, including ways they can mitigate the cost of new equipment, as well as the maintenance and calibration requirements to make sure those tools remain fit for purpose.
When we consider just what press fit systems have to offer, it’s no surprise that they are seeing a surge in growth. With product development constantly evolving, those forward-thinking installers should always be on the lookout for more innovative and costeffective ways of working.
Antony Corbett is product manager for Geberit