Remote reaction
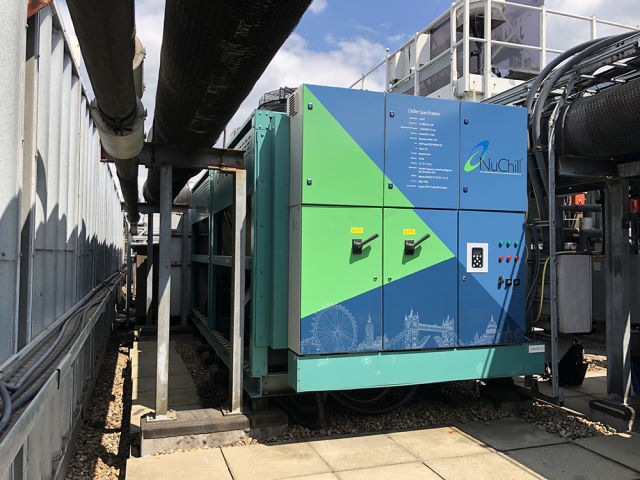
Trevor Dann explains the benefits of remote diagnostics and energy management for the data centre cooling market.
Of all users of cooling equipment, machinery used to support data and IT cooling is among the most crucial in terms of continuous availability requirement. This means selection of reliable equipment from the outset, but as any equipment ages its reliability will reduce.
This is where the real test of equipment quality comes into question. However, once a breakdown has occurred the next and immediate problem is what can be done, and quickly, to resolve the situation?
Developing from the very technology many data centres now provide to the market, and in particular the concept of the “Internet of Things”, an increasing use of remote access technology can provide a unique service solution to enable the swiftest of reaction when critical plant fails.
Harnessing the power of the IoT allows service companies to ensure full service access to our chillers while they operate on site. This enables the offsite maintenance team to not only observe what is happening with a specific chiller, air handling system or pump system, but also to adjust, reset and even routinely monitor performance.
However, for many IT-related premises there is a separate and critical concern for a high level of data access security. Using the internet to access a machine can present an unacceptable external access node for would-be troublemakers, hackers and their kin.
The GDPR introduced in May 2018 is now starting to make its regulatory presence felt, with huge fines for organisations that allow breaches of personal data. In view of this it is vital that remote monitoring systems can offer appropriate levels of security. For example, Thermozone’s RODEM system (Remotely Operated Diagnostic and Energy Management), uses the mobile phone 3G and 4G systems that are widely available as a means of access.
The 3G and 4G networks operate completely separately to installed data networks and for most sites, someone with a mobile phone in their pocket is not considered a data security hazard. Effectively hooking a chiller or indeed other item of building service support equipment up to its own mobile phone provider is no different.
Once established, we can log in to specific machines and then observe operation. Access typically is established in around one minute, and once logged in the same access is available, from any Wifi hotspot as if plugged in via a fixed cable at the machine itself.

Remote access can also support better ongoing maintenance. It is possible to undertake monthly remote virtual inspection of chillers allowing for a of review the running operation, including any trips of alarms. The remote monitor team can also adjust for optimum seasonal efficiency, notiung any deleterious trends. Record files can also be downloaded for client records.
Reviewing specific chillers (or other equipment) in this way soon builds up an operational footprint, where any issues that may occur quickly stand out, allowing an approach to resolve nuisance issues early, before they become system failures. If conducted correctly, the remove monitoring can also reduce the need for more costly on-site call-outs.
Of course, things can go wrong on-site and swift action is required especially in summer as temperatures rise. Again, remote monitoring is ideal for the data centre market, allowing engineers to observe the issue within minutes – rather than requiring a longer wait for an on-site visit. And where a physical presence is required to fix a problem, remote monitoring means that an engineer arrives on site with a much better idea of what the problem is – and where. We estimate that around 85% of call outs are now entirely resolved remotely.
The latest version of our own system, RODEM 2, initiates an email alert immediately a machine goes into fault. We receive an email within seconds of the fault alarm, however with our own system most alarms are on a ‘two strikes and out’ mode, so we then expect to see a self-reset after 10 minutes.
For clients using remote monitoring (and for those offering these services) terms of service are important to establish and understand on both sides. Understandably, clients want to remain in control of service expenditures as much as possible. However, in the case of a machine-generated ‘virtual call out’, the first a client may now is after the call is process – thereby incurring a cost.
This requires a clear understanding and agreement to sensible commercial rules. We overcome this by establishing a pre-agreement as to how we should react to a virtual call out: Log In first and report later; or report an alert first then only log in after due authorisation. Clearly the first option allows for swifter reaction but offering both methods allows the client to retain the desired level of expenditure control.
Trevor Dann is director of Thermozone